Společnost Siemens se zapojila do projektu iniciovaného Českým institutem informatiky, robotiky a kybernetiky ČVUT v Praze (CIIRC ČVUT) a v závodě Siemens Elektromotory Mohelnice vyrábí na speciální 3D tiskárně respirační polomasky a jejich části, které chrání před nákazou koronavirem SARS-CoV-2. Tyto polomasky, kterých lze v Mohelnici denně vyrobit více než 40, mají certifikaci podle normy EN 140:1999 a dosahují tak stejného, resp. Vyššího stupně ochrany než respirátor filtrační třídy FFP3. Projekt ochranné polomasky je prvním tzv. use case pro ověření konceptu distribuované výroby.
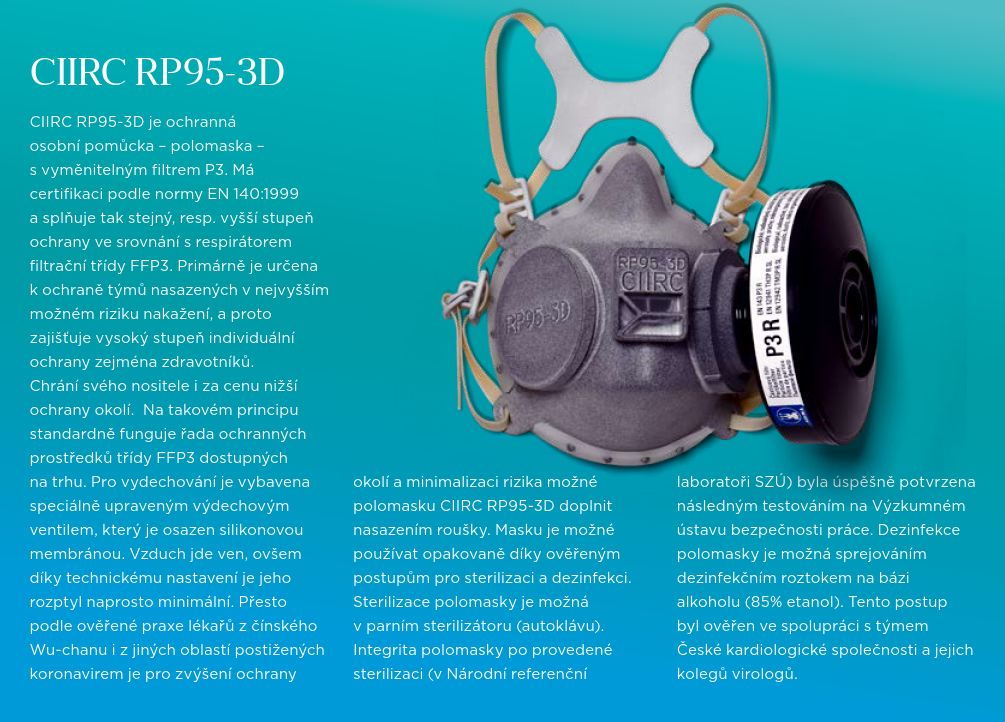
Respirační polomasku CIIRC RP95-3D na ochranu proti koronaviru vyvinul, jak již její název napovídá, CIIRC ČVUT, a to během pouhého jednoho týdne. Obvykle přitom takovýto vývoj trvá několik měsíců. „V tomto případě vývoje ochranné polomasky se podařilo skloubit tři základní věci – tým špičkových výzkumníků, nejmodernější výzkumnou infrastrukturu a cenná partnerství, která již dlouhodobě CIIRC ČVUT pěstuje mezi akademickými i průmyslovými organizacemi,“ shrnuje předpoklady tohoto bleskurychlého vývoje prof. Vladimír Mařík, vědecký ředitel CIIRC ČVUT. „Přesto je to v určitém směru i pro náš institut nová zkušenost, zejména pokud jde o opravdu raketovou realizaci transferu technologií z vysoké školy do průmyslové výroby. Ostatně o to se stará nový univerzitní start-up, společnost TRIX Connections,“ dodává.
Ohlas i ze zahraničí
Certifikační proces – podmínka uvedení respirátoru do praxe – probíhal díky doporučení Evropské komise a nouzovému stavu ve zrychleném řízení na půdě Výzkumného ústavu bezpečnosti práce v Praze. Kvůli tomuto zkrácenému řízení má také certifikace jen omezenou platnost – na tři měsíce a jen pro území České republiky. Tým vývojářů má však v plánu získat i plnohodnotnou certifikaci pro celou EU, která je uznávána i v USA. Ostatně respirátor RP95-3D již v zahraničí vzbudil ohlas, a to nejen v médiích, ale i v odborných kruzích či inovačních komunitách. Například portál HubHub zařadil masku mezi pět inovativních evropských projektů, které pomáhají v boji proti koronaviru. Samotnou výrobu respirátorů, jejichž základní část (tělo polomasky s komponenty) se tiskne na 3D tiskárně HP Multi Jet Fusion, v celé České republice koordinuje společnost 3Dees Industries, oficiální zástupce HP 3D Printing pro Českou republiku. Pod jejím dohledem probíhá také následná montáž komponentů – těla masky, silikonového těsnění, silikonové membrány, filtru Sigma P3 a upínacích pásků.
Pro ty v první linii
Do poloviny května, kdy tento článek vznikl, bylo Ministerstvu zdravotnictví ČR předáno přes 3 000 respirátorů. Všechny respirační polomasky, které touto cestou vznikají, poskytuje ministerstvo lékařům, sestrám a dalším pracovníkům ve zdravotnictví, kteří s koronavirovou pandemií bojují v první linii. „Lékaři a zdravotníci v první linii respirátory nutně potřebují, aby mohli pomáhat těm, kdo onemocněli nemocí covid-19. Právě oni jsou pro nás všechny tou největší nadějí a považuji za morální povinnost je v rámci našich možností podpořit,“ říká ředitel závodu Siemens Elektromotory Mohelnice Pavel Pěnička. V závodě Siemens Elektromotory Mohelnice se nachází jedna z pouhých sedmi 3D tiskáren na území České republiky, které jsou vybaveny technologií Multi Jet Fusion. Tato špičková technologie se vývojářům z CIIRC po řadě testů nakonec ukázala být pro tisk respirátorů tou nejvhodnější. „S výrobou respirátoru podle návrhu ČVUT jsme začali jako jedni z prvních,“ říká Michal Průša, který 3D tisk v mohelnickém závodě zaštiťuje, k zapojení společnosti Siemens do projektu. Aktuální koronavirová pandemie je podle něj velkou zkouškou převážně rychlosti a univerzálnosti výroby. „Již teď dostávám informace, že o 3D tiskárny začíná být mnohem větší zájem než dříve, a to především ze strany podnikatelských subjektů. Tento zvýšený zájem je samozřejmě zapříčiněn takřka neomezenými možnostmi 3D tiskáren a naprostou časovou a výrobní výhodou právě v době takovéto krize. Bohužel do vypuknutí pandemie byly možnosti 3D tisku spíše chápány povrchově, avšak s vypuknutím pandemie se také rozjela i velká mediální kampaň na využití 3D tiskáren, které opravdu v krátkém čase zachraňovaly doslova životy,“ popisuje změnu ve vnímání 3D tisku Michal Průša.
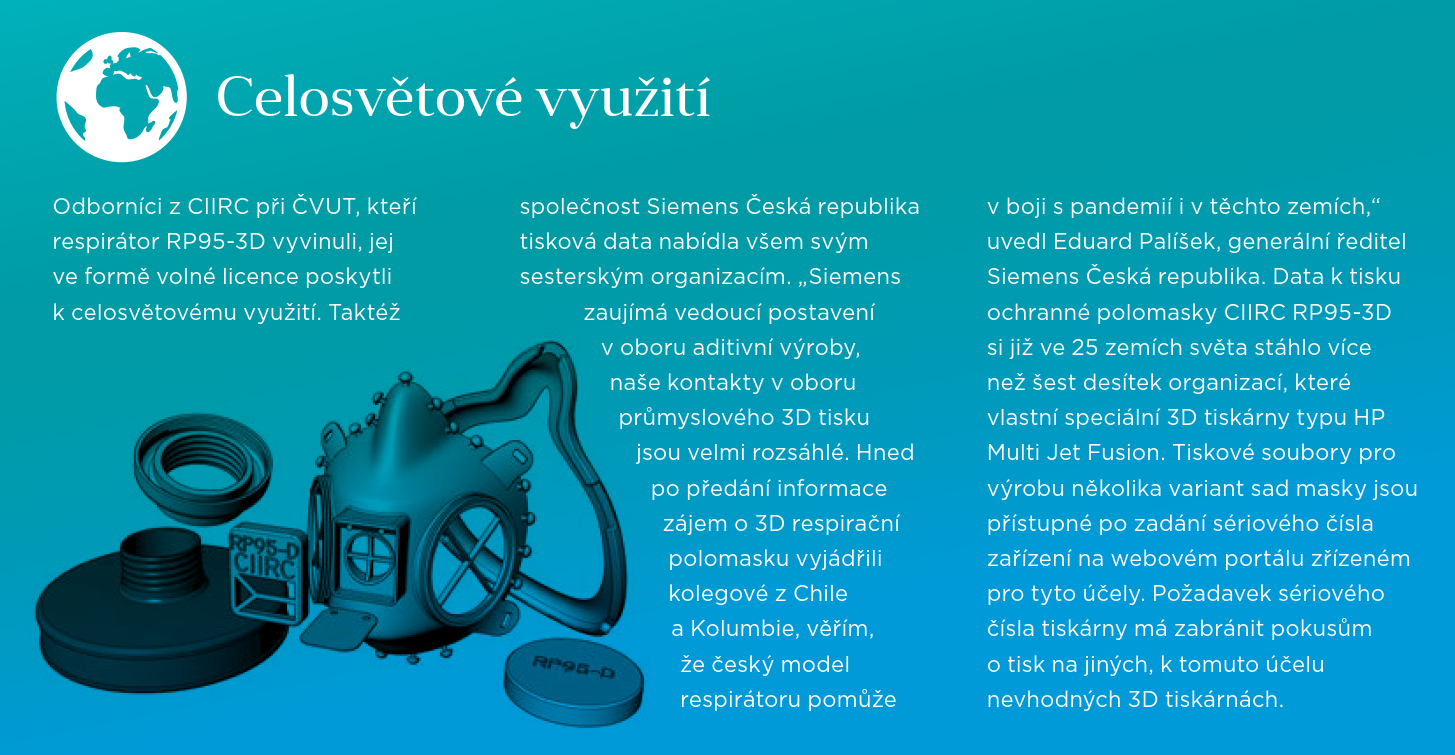
„Lidé si začali uvědomovat možnosti a výhody 3D tisku pro své firmy, a to i za cenu větších pořizovacích nákladů, které v případě profesionální průmyslové technologie jdou až do několika milionů korun,“ dodává. Na tuto stranu cenového spektra patří i tiskárna HP Multi Jet Fusion. Výroba v ní probíhá tak, že plastový prášek se spojuje speciálními pojivy, a takto vzniklý produkt je následně vytvrzen vysokoenergetickým infračerveným zářením. Za normálních okolností tato technologická novinka nachází uplatnění zejména v nástrojárnách, v těchto dnech však tiskne přes 40 kusů respirátorů nebo několik stovek drobných dílů do respiračních polomasek denně. Díky preciznímu provedení lze polomasky používat neomezeně a filtry, kterými polomasky osazuje Sigma Lutín, vydrží v závislosti na okolním prostředí a individuální zátěži až několik dní.
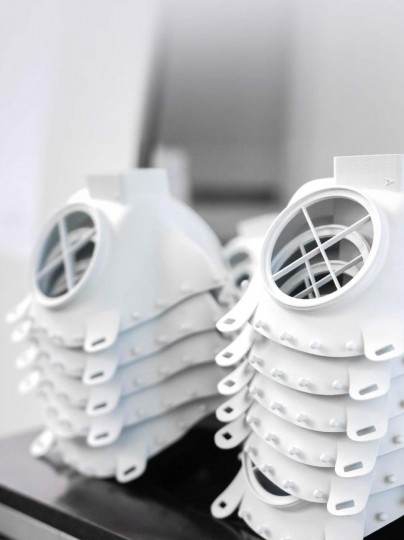
Co je technologie HP Multi Jet Fusion
Podle výhradního distributora 3D tiskáren HP Multi Jet Fusion v České republice – společnosti 3Dees Industries – se jedná o jedinou technologii 3D tisku, která je schopna nákladově konkurovat tradiční sériové výrobě plastových dílů. Tato technologie umožňuje prototypovat a vyrábět tvarově stálé a vysoce přesné objekty, a to až desetkrát rychleji a při polovičních nákladech v porovnání s doposud známými nejproduktivnějšími 3D technologiemi. Předností 3D tiskáren HP Multi Jet Fusion je rovněž to, že HP u nich podporuje tzv. otevřenou materiálovou platformu (HP Multi Jet Fusion Open Platform). To znamená, že výrobce plastů, který se rozhodne vyvíjet materiál pro tyto tiskárny a následně získá patřičnou certifikaci, může materiál dodávat přímo spotřebiteli. Aktuálně s HP spolupracují největší firmy v oboru, jako jsou Henkel, BASF, Arkema či Evonic. Závod Siemens Elektromotory Mohelnice má od září loňského roku k dispozici 3D tiskárnu HP Multi Jet Fusion 540. Ta do současnosti vytiskla již stovky různých přípravků a dílů. Jednalo se například o přípravek využívaný při montáži svorkovnicových zátek kolaborativním robotem. Výroba 12 kusů trvala 3D tiskárně 48 hodin, klasické nástrojárně přitom trvá vyrobit toto množství více než dvakrát déle. Nahrazení kovu plastem tak kromě významné finanční úspory znamenalo i značné odlehčení přípravku a usnadnění manipulace s ním. Další pěknou ukázkou možností této 3D tiskárny byla výroba přípravku na ukládání hřídelí pro stroj EMAG. Ty se nyní po provedení tvarově-provozní optimalizace do nového pásového dopravníku ukládají horizontálně, a nikoli vertikálně jako doposud. Při výrobě 100 kusů těchto přípravků vychází 3D tisk desetkrát levněji než klasická, subtraktivní výroba. Časová úspora je rovněž značná – 3D tisk je oproti výrobě v nástrojárně až sedmnáctkrát rychlejší.
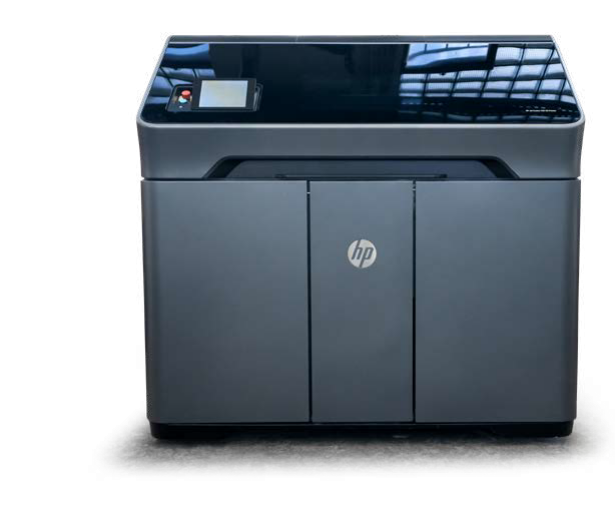