Testbed pro Průmysl 4.0 v pražských Dejvicích je prvním zařízením svého druhu u nás. Nejen o něm, ale i o spolupráci akademické a průmyslové sféry i o unikátních řešeních Siemens, která tvoří srdce i mozek celé laboratoře, jsme si povídali s Ing. Pavlem Burgetem, Ph.D., vedoucím Testbedu pro Průmysl 4.0 Českého institutu informatiky, robotiky a kybernetiky.
Jak vznikla myšlenka vybudovat v Praze v rámci ČVUT první český Testbed?
Nápad vznikl na základě spolupráce ředitele Českého institutu robotiky a kybernetiky (ČIIRK) profesora Vladimíra Maříka a jeho německého kolegy profesora Wolfganga Wahlstera z Institutu pro umělou inteligenci v Saarbrueckenu (DFKI), který je duchovním otcem myšlenky Průmyslu 4.0 v Německu. Profesor Mařík je hlavním propagátorem myšlenky Průmysl 4.0 v České republice a vedoucím týmu, který připravoval vládní iniciativu Průmysl 4.0. Cílem obou institucí je právě budování testbedů a jejich vzájemné propojení.
V Německu již nějaké testbedy fungují? Jaká je tam situace?
Ano, několik laboratoří je např. na univerzitách v Saarbrueckenu, Aachenu, Stuttgartu a dalších. Budování testbedů je plně v kontextu rozvíjení myšlenky Průmyslu 4.0. Zaměřují se na různé oblasti, některé jsou vyloženě experimentální, jiné se více přibližují průmyslové výrobě. Společným prvkem je snaha zkoumat nové možnosti a metody, jak reálně použít principy Průmyslu 4.0.
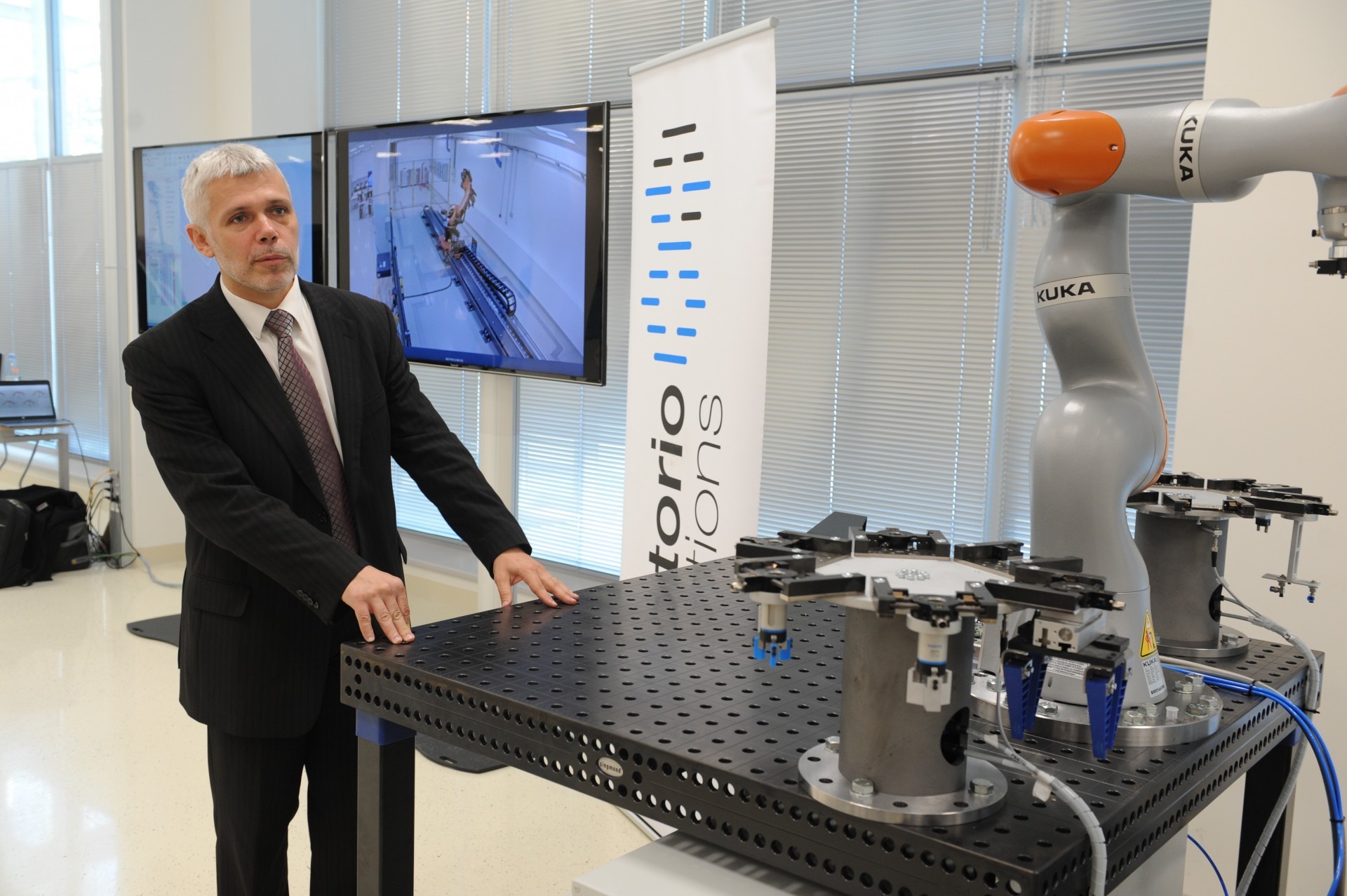
Pro koho je vlastně váš Testbed určen?
Testbed bude sloužit vědeckému výzkumu, výuce studentů a soukromým firmám pro testování nových technologií před nasazením v praxi. Zkoumáme nové směry vývoje digitálních technologií a snažíme se s nimi seznámit odbornou veřejnost a uvádět je do praxe.
Na co se hodláte specializovat?
Nabízí se velký prostor pro výzkum optimálního rozvrhování a plánování, například prostřednictvím multiagentních systémů neboli vzájemně propojených strojů, které si zachovávají určitou míru autonomie a navzájem se domlouvají. Tato oblast nám přijde velmi zajímavá, neboť zohledňuje myšlenku flexibilní výroby a podporuje „přizpůsobivost“ strojů tomu, co je zrovna zapotřebí vyrábět. Z tohoto principu vychází i výrobní linka v Testbedu v Praze, kterou bude možné flexibilně upravovat a rozšiřovat podle toho, co se na ní zrovna bude vyrábět. Do linky jsou zapojené reálné i virtuální stroje a roboty, které vzájemně spolupracují. Vedle reálné linky máme nasimulované i její digitální dvojče a veškerá zapojená zařízení dokážeme zprovoznit také virtuálně.
Jak je laboratoř velká?
Testbed se rozkládá ve dvou podlažích. V přízemní je instalovaná výrobní linka s dopravníkem a robotem KUKA spolupracujícím s člověkem, v suterénní laboratoři jsou velké roboty a obráběcí centra. Obě části linky jsou propojené a vzájemně spolu komunikují prostřednictvím sítě Profinet.
Spodní část laboratoře se však více profiluje na operace obrábění a kromě robotů se specializuje na obráběcí stroje, jejich modelování, diagnostiku a optimální řízení. Horní část laboratoře se zaměřuje především na operace montáže, adaptivní rekonfigurace strojů, autonomní roboty a spolupráci robotů s člověkem. Obě laboratoře jsou zapojeny do systému správy životního cyklu výrobku a mohou navzájem pracovat například jako subdodavatelé v dodavatelském řetězci koncového výrobce.
Zmínil jste digitální dvojče – v jaké podobě ho v Testbedu nalezneme?
Digitálních dvojčat máme v laboratoři celou řadu, dá se říci, že ke každému reálnému zařízení nebo procesu máme i jeho virtuální kopii. Simulační prvky totiž tvoří ve výrobní lince Testbedu stejně důležitou součást jako ty reálné. Jen díky nim pak můžeme dosahovat kýžené efektivity a flexibility nejen provozu, ale i dalších fází životního cyklu výrobku.
Jedním z hlavních partnerů Testbedu na ČIIRK a také zakládajícím členem iniciativy Národní centrum Průmyslu 4.0 je společnost Siemens. Proč jste si ke spolupráci vybrali právě tuto firmu?
Společnost Siemens pokrývá svými nástroji většinu oblastí, které Průmysl 4.0 zasahuje. Jednou z důležitých věcí jsou produkty PLM Software a jejich nástroje pro návrh produktu, simulace na různých úrovních, generování dat pro výrobu, příprava výrobního postupu, samotná příprava a simulace technologie.
Dále je zde široké portfolio řešení pro automatizaci výroby z rodiny řídicích systémů Simatic a jejich propojení se simulačními prostředky. Simulaci lze díky tomu řídit přímo z PLC systémů a kombinovat ji s reálnými prvky. Všechno přitom funguje perfektně dohromady díky vzájemné propojitelnosti a integraci dílčích komponent. V takovéto šíři záběru řešení a nástrojů nemá Siemens na trhu konkurenci. Navíc je právem považován za lídra na poli inovací a vizionáře v dalším vývoji konceptu Průmyslu 4.0.
Budete využívat nástroje Siemens také pro sběr a analýzu dat ze strojních zařízení a výrobních procesů?
Ano a byl to i jeden z našich hlavních požadavků na dodavatele systému, aby dokázal tato data sbírat a předávat k dalšímu zpracování. Hodně si slibujeme například od sledování spotřeby elektrické energie a návrhů řešení, jak dosáhnout výrazných úspor např. uváděním momentálně nečinných strojů do režimu stand-by. Princip je stejný, jako když uspíte počítač, na němž právě nepracujete. Podle zatím dostupných měření a analýz je možné ušetřit uváděním strojů – například robotů na montážních linkách – do režimu stand-by 10 až 15 procent energie z celkové spotřeby.
Jak uspávání strojů funguje v praxi?
Uspání a probuzení může probíhat poměrně rychle a navíc stroj dostane včas signál, aby se probudil a připravil k výkonu, takže se může plynule zapojit od práce. Uspávání je tak mnohem výhodnější než úplné vypnutí stroje, protože zachovává flexibilitu provozu.
Lze režim stand-by použít i pro starší stroje nebo je to doménou pouze nových zařízení?
Režim stand-by lze úspěšně instalovat i do starších strojů, např. úpravou řídicího systému a použitím moderních frekvenčních měničů. Pro provozovatele starších výrobních technologií je také velmi vhodné virtuální zprovoznění stroje a data monitoring. Tam mohou získat opravdu nečekaně velkou úsporu díky tomu, že se dozví detailní informace nejen o stroji, ale i o celé výrobní technologii a jejích rezervách. A to je právě jedna z úloh Testbedu: ukazovat firmám v praxi možnosti, které digitalizace výroby přináší a které by jim mohly pomoci zvýšit flexibilitu a efektivitu výroby a tím urychlit uvádění nových výrobků na trh.
Co vidíte jako hlavní oblast, které by se české průmyslové podniky měly více věnovat?
Obrovský, zatím nevyužitý potenciál vidím ve sběru a následné analýze dat získaných z výroby. Pomocí speciálně vytvořených algoritmů nebo matematických modelů lze odhalit mnoho důležitých informací a zlepšit třeba včasnou diagnostiku hrozících poruchových stavů a naplánovat odstávku nebo servis stroje dřív, než dojde k poškození dílu. Stejně tak je velký potenciál v digitalizaci jednotlivých stupňů hodnotového řetězce a v postupném zavádění digitálního dvojčete výrobku a výrobního procesu.
Jaké komponenty Siemens v Testbedu používáte?
Hlavním řídicím systémem je PLC Simatic S7-1518, do linky jsou ale kvůli modularitě zapojeny i menší řídicí systémy Simatic S7-1512, které ovládají jednotlivá připojená zařízení. Pro vizualizaci používáme HMI dotykové panely. Pro obrábění používáme Sinumerik nejen s tradičními obráběcími stroji, ale také s obráběcími roboty. Pro komunikaci používáme Profinet, k dispozici je také protokol OPC UA pro budoucí rozšiřování o další řídicí systémy. Samozřejmostí je použití softwarových nástrojů Teamcenter, Tecnomatix, NX, TIA Portal, Information Server a dalších. Velký důraz klademe na využití diagnostických prostředků, ať už se jedná o diagnostiku komunikace Profinet, diagnostiku samotných zařízení nebo sledování provozních podmínek strojů, tzv. condition monitoring. Do budoucna uvažujeme o zařazení například lineárních samostatně řiditelných pohonů Sinamics a zavedení nástrojů Simatic IT pro řízení a optimalizaci výroby.
V čem vidíte největší přínos Siemensu pro projekt Testbed?
U Siemensu je vidět, že se snaží jednotlivé nástroje pro Průmysl 4.0 integrovat dohromady do jednoho plně kompatibilního řešení. To na jedné straně zahrnuje vývojářské programy od PLM Software přes koncept TIA používaný v průmyslové automatizaci, po chytrou továrnu se všemi digitálními a virtuálními komponentami až po manažerské a nadřazené systémy. Vedle toho nesmíme zapomínat na cloudové řešení MindSphere pro sběr a analýzu velkých dat s integrovanými možnostmi sběru dat z průmyslových i jiných procesů.
Kam podle vás směřuje vývoj českého průmyslu? Čekají nás velké změny?
Podle mého názoru lze čekat stále zřetelnější nástup digitalizace na různých stupních hodnotového řetězce výrobku a stále výraznější podíl strojů při vykonávání monotónní práce. Stále více se budou projevovat prvky umělé inteligence ať už v oblasti rozpoznávání a zpracování obrazu, vyhodnocování provozních dat nebo v oblasti různých expertních systémů podporujících rozhodování.
Automobilový průmysl si nejspíše zachová svou vůdčí pozici, ostatně už nyní je v mnoha oblastech lídrem digitalizace a inovací. Kromě toho můžeme očekávat větší podíl robotizace a autonomního zpracování v takových činnostech, kde dosud převládala manuální práce.