Výroba společnosti Siemens v moravské Mohelnici má dlouhou tradici. Začala již ve dvacátých letech minulého století, tehdy pod značkou Siemens Elektrotechnika. Na tuto tradici dnes důstojně navazuje závod na výrobu přípojnicových systémů nesoucí název Siemens Busbar Trunking Systems (SBTS).
Na počátku nového milénia postavila společnost Siemens v Mohelnici na zelené louce továrnu na výrobu přípojnicových systémů se záměrem doplnit své portfolio a moci v daném průmyslovém segmentu nabízet kompletní řešení. Výrobní závod se kromě přímých dodávek zákazníkům stal také součástí portfolia TIP (Totally Integrated Power), což je program, jehož cílem je nabízet kompletní řešení budov, počínaje jejich připojením k fotovoltaické elektrárně přes instalaci trafostanic a rozvaděčů až po samotné rozvody uvnitř budov k nejrůznějším typům spotřebičů. Přípojnice hrají v tomto řetězci velmi důležitou roli, oproti klasické kabeláži totiž mají několik podstatných výhod. Jejich montáž je poměrně snadná a rychlá, a to i v případě složitějších rozvodů. Nepoužívá se při ní totiž žádné speciální nářadí a díly není možné vzájemně chybně propojit. Prostorové nároky přípojnic jsou v porovnání s kabely výrazně menší. Minimální jsou též jejich nároky na údržbu. Přípojnicové rozvody lze rovněž následně velmi snadno upravovat či rozšiřovat.
Pokud například potřebujete změnit lokaci výrobního stroje, provedete ji zcela prostě jen jeho posunutím a jednoduchou instalací odbočné skříně v jeho bezprostřední blízkosti, a to bez nutnosti odstavení dodávky elektrické energie do okolních spotřebičů. S kabely toto provádět nelze, navíc svazky kabelů bývají často velmi nepřehledné, takže jen rozpoznání toho správného může činit potíže. Ve srovnání s kabelovými rozvody jsou přípojnice také odolnější proti ohni. V případě požáru tak umožňují delší dobu napájet například nouzové osvětlení nebo požární čerpadla. Při jejich hoření se také neuvolňují žádné nebezpečné plyny.
99 % produkce mohelnického závodu jde na export, především do Německa a Nizozemska
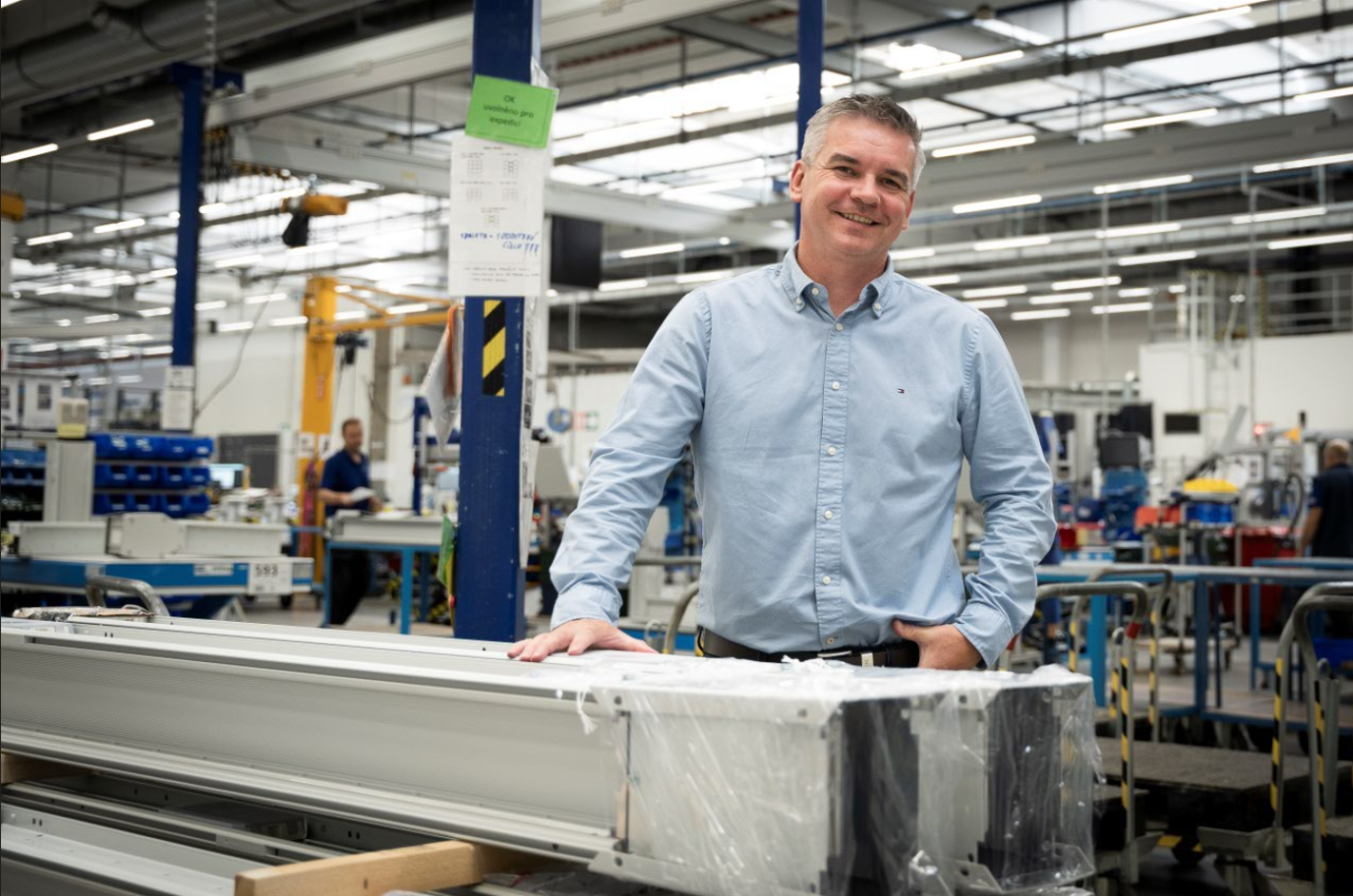
SBTS Mohelnice
má ve světě několik sesterských závodů. V Evropě se jeho sesterský závod nalézá v Kolíně nad Rýnem, celosvětově pak je další ještě ve Vietnamu. V Číně má Siemens také joint venture. Pod značkou Siemens se vyrábějí také pryskyřicové přípojnice LR ve Švýcarsku. V tomto
případě se jedná o speciální typ přípojnic určený pro instalace v extrémních podmínkách, například v chemických provozech.
Významným momentem v historii závodu byl rok 2015, kdy byla na trh
uvedena přípojnice s typovým označením LI. Tu si totiž společnost Siemens již vyvinula sama na základě zpětné vazby z trhu. Tento nový model tehdy nahradil přípojnici LX. Mezi jeho hlavní přednosti patří vyšší zkratová odolnost (120 kA), lepší krytí (IP55) a stálost proudového přenosu. Na vzniku této přípojnice
spolupracovali čeští vývojáři se svými
kolegy z Německa. „Krytí podle standardu IP55 je dnes samozřejmostí, my nabízíme
i úroveň IP66. Projektanti totiž často
v projektech uvádějí velmi vysoké nároky na odolnost vůči prachu či vodě,“ říká ředitel mohelnického závodu SBTS Ing. Petr Mazal.
Co se týče amperáže, vyrábějí se v Mohelnici hlavně přípojnicové systémy s kapacitou 1600 A, 2000 A a 2500 A a jejich dvojčata, resp. systémy s dvojnásobnou kapacitou.
Od akvizic po největší závod
Své portfolio v oblasti přípojnicových systémů začal Siemens budovat především prostřednictvím akvizic a relokací. V případě mohelnického závodu se nejprve jednalo o relokaci přípojnicového systému LX – původně do výrobní haly mohelnického závodu Siemens na výrobu elektromotorů, protože samostatná hala na výrobu přípojnic se teprve budovala. Krátce po jejím uvedení do provozu na přelomu let 2005 a 2006 byla do Mohelnice přemístěna i výroba přípojnicové řady BD2 ze sesterského závodu v Kolíně nad Rýnem. Celý relokační projekt byl završen v roce 2008, kdy byla do Mohelnice přenesena portfolia CDK a BD01. Tím byl dokončen plán tohoto závodu vyrábět na čtyřech výrobních linkách čtyři různé produkty. V současné době má Siemens v Mohelnici největší závod na výrobu přípojnicových systémů v Evropě. Pracuje v něm kolem 280 zaměstnanců.
Vstříc zákazníkům
Jednou z hlavních dlouhodobých snah mohelnického závodu je zvyšování efektivity procesů. Jinými slovy: vedení závodu usiluje o to, aby výroba nebyla závislá jen na dodavatelských řetězcích a mohla tak lépe a flexibilněji reagovat na požadavky zákazníků. „Začínali jsme jako typická montážní firma, ale postupně zavádíme i výrobu vlastních komponentů. V současné době máme vlastní práškovou lakovnu, vysekávací technologie a nedávno jsme implementovali robotické svařování vodičů,“ popisuje kroky směrem k větší soběstačnosti a efektivitě Petr Mazal. Vedle ceny je totiž pro mnoho zákazníků stejně klíčový i dodací termín. A zmíněné modernizační kroky velkou měrou přispívají k tomu, že závod dokáže i v tomto ohledu drtivé většině zákazníků vyhovět. Díky vybudování již zmíněné práškové lakovny v roce 2020 došlo k dalšímu posílení výroby plechových dílů. Siemens tak dnes nenabízí pouze standardizované výrobky, ale dokáže ve velmi krátkém čase vyhovět i značně specifickým požadavkům zákazníků, ať již jde o speciální design, nebo malovýrobu čítající pouze jednotky kusů.
Došlo tak ke zvýšení flexibility a rychlosti výroby plechových dílů, na kterých se obvykle odehrává nejvíce úprav. „Podařilo se nám odstranit rozdíl mezi termíny dodání ve výrobě standardních a speciálních řešení,“ shrnuje výrobní změny Petr Mazal. Přípojnicové systémy společnosti Siemens se hojně používají na letištích, neobejde se bez nich například londýnské Heathrow. Instalují se rovněž ve velkých hotelech či výškových budovách, v průmyslových areálech nebo v datacentrech. Vybaveno je jimi například největší rakouské datacentrum nacházející se ve Vídni.
V současné době Siemens plánuje začít nasazovat své přípojnicové systémy i v oblasti nabíjecích stanic pro elektromobily. Například v německém Řezně již přípojnice Siemens slouží v nabíjecích stanicích pro elektrobusy tamního provozovatele městské hromadné dopravy. „Vedle provozovatelů městské hromadné dopravy se však snažíme vyjít vstříc i nákladním dopravcům, kteří začínají budovat vlastní elektroflotilu,“ doplňuje Petr Mazal.
Vlajková loď
Vlajkovou lodí mohelnického výrobního závodu je přípojnice s označením LI. Ta je schopna vést proud o velikosti až 6300 A. V současné době tvoří drtivou většinu produkce závodu. Unikátní je především tím, že nabízí proudovou kapacitu 5 000 A s hliníkovými vodiči. To oproti dříve používané mědi samozřejmě znamená podstatně nižší hmotnost přípojnice i její cenu. Aktuálně jsou tato i další typy přípojnic žádány s tzv. sendvičovým systémem, tzn. jeden vodič je položen přímo na druhém vodiči a k chlazení se nepoužívá vzduch. Díky tomu má tento systém vyšší IP rating. Velmi žádaný je především na asijském trhu, kde je v řadě oblastí značně vysoká vlhkost vzduchu, která může elektrickým rozvodům způsobovat vážné technické problémy.
Nejnovějším přírůstkem do rodiny přípojnic je typ LData z řady SIVACON, který byl vyvinut speciálně pro datová centra. Na trhu je od loňského roku a technologicky vychází ze systému LD. „Tento typ vznikl na základě požadavku datových center, která tvoří značnou část našich zákazníků. Každý rack datového centra totiž potřebuje vlastní napájení, přičemž jednotlivé racky jsou od sebe standardně vzdáleny 60 cm. Náš systém umožňuje instalaci odbočných skříní v rozestupech v řádu jednotek centimetrů, takže je maximálně flexibilní a potřeby datacenter plně uspokojuje.
Některá datacentra dokonce takto vysokou míru flexibility ani nevyužijí,“ usmívá se Petr Mazal. Dodejme, že samotné přípojnice tohoto systému se vyrábějí v Kolíně nad Rýnem, v Mohelnici vznikají jeho odbočné skříně. Odbočné skříně, nedílná součást přípojnic, bývají osazeny i různými ovládacími a bezpečnostními prvky. Ovládací prvky v odbočné skříni je dnes možné ovládat i dálkově pomocí sběrnic, jejichž rozvod je součástí sběrnicového systému.
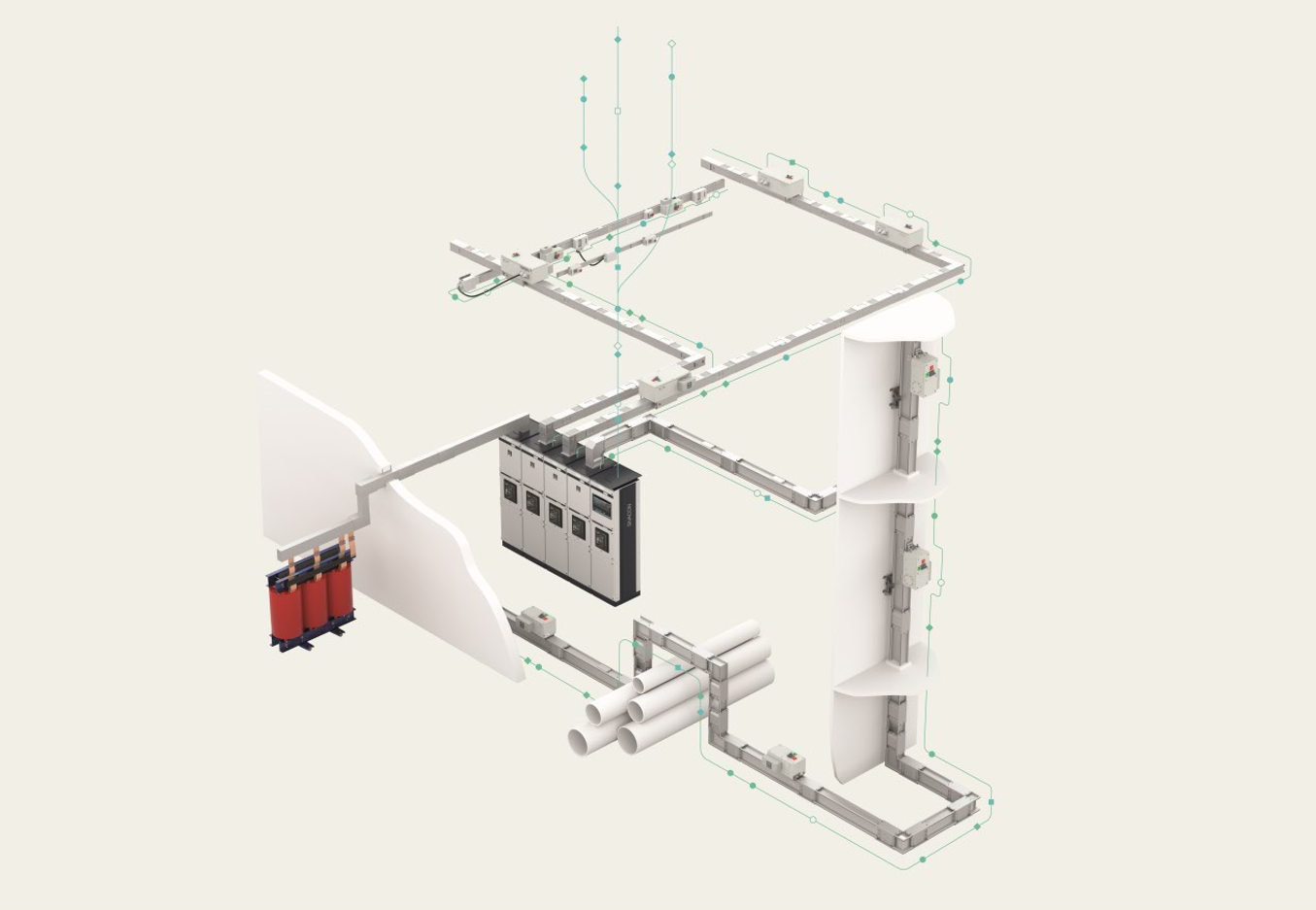
Přípojnicové krytí: V kódovém označení míry krytí značí první číslice ochranu proti vniknutí pevných částic. Jejím intervalem je stupnice 0 až 6. Druhá číslice označuje ochranu proti vniknutí kapaliny a pohybuje se na škále od 0 do 9. IP55 tedy nabízí střední úroveň ochrany, která však v obvyklých provozních podmínkách plně vyhovuje
Vývoj pokračuje
K nejvýraznějšímu pokroku v oblasti přípojnicových systémů dochází v současné době ve vybavení odbočných skříní. Jedná se v podstatě o malý rozvaděč, který měří průtok proudu či odpor a naměřená data odesílá k dalšímu zpracování. „Proto byla také vybudována zkušebna. Hotový, plně osazený výrobek v ní ihned odzkoušíme a odzkoušený výrobek opatřený certifikátem o zkoušce předáme zákazníkům,“ říká Petr Mazal. Požadavky trhu podle něj nyní míří především na rozšiřování, resp. volitelnost funkcionalit.
Největším úkolem vývojářů proto aktuálně je, aby ze standardních dílů bylo možné vytvářet specifické konfigurace, tj. aby si zákazník mohl sám nakonfigurovat produkt podle svých potřeb. Právě k tomu lze velmi dobře využít digitalizovaných komponentů ve vybavení přípojnic. Samostatná datová linka přitom není potřeba, protože speciální datové zařízení PowerLine umožňuje posílat základní provozní data přímo po vodiči. Vývoj pokračuje také v oblasti elektromobility. Kolegové v Německu nyní intenzivně pracují na vývoji wallboxů, které již nebudou potřebovat kabeláž, ale budou zásobovány proudem přes přípojnici.
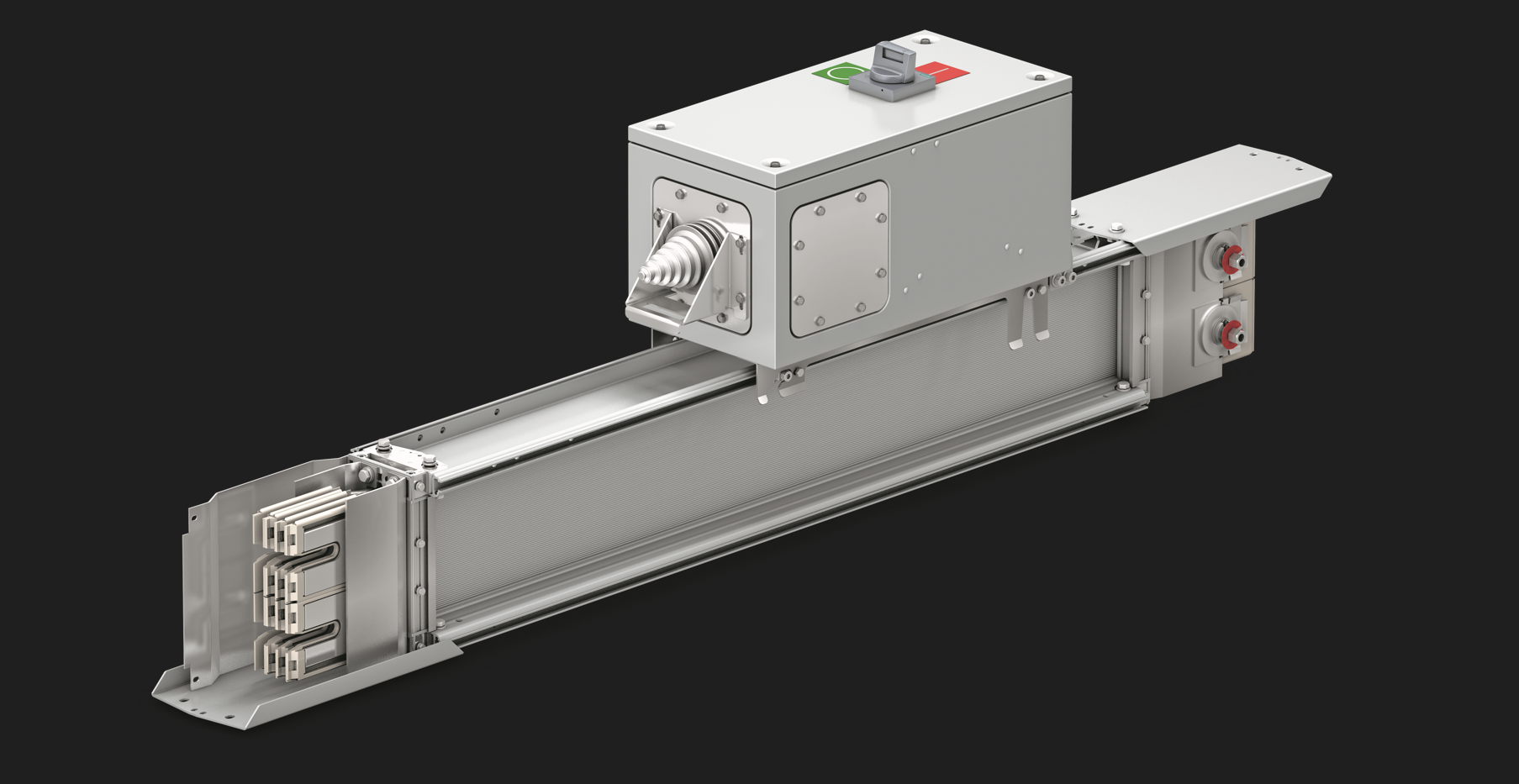
V Mohelnici vznikají i komponenty pro větrné elektrárny s typovým označením SG11, které vyrábí společnost Siemens Gamesa. Kompletní řešení pro ně zajišťuje výrobková řada LD, která je vyráběna v Kolíně nad Rýnem. V současné době se již dokončuje vývoj jednotek SG14, taktéž s přípojnicovými systémy Siemens. Na trhu by se tyto elektrárny měly objevit počátkem roku 2024.
Významné momenty v historii závodu SBTS Mohelnice
2004 – převzetí závodu na výrobu přípojnicových systémů od společnosti Moeller
2005 – otevření nové výrobní haly
2015 – uvedení na trh nové, vlastní produktové řady s označením LI
2020 – rozšíření portfolia o vlastní předvýrobu komponentů
2022 – zprovoznění zkušebny pro certifikaci rozvaděčových (odbočných) skříní
2023 – instalace prvního robotického pracoviště na svařování hliníkových prvků a zahájení dekarbonizačního projektu
Udržitelnost mezi prioritami
Společnost Siemens bere svou roli, kterou přijala v celoplanetárním snažení o udržitelnost, velmi vážně. A plně to platí i pro výrobní závod v Mohelnici, který plánuje dosažení uhlíkové neutrality do roku 2030. „V první fázi jsme přeměnili plynové vytápění administrativní budovy na elektrické. Nyní chystáme instalaci tepelných čerpadel a fotovoltaické elektrárny. Na střeše závodu máme klimatizační jednotky, které umějí i vytápět. Těmito kroky jsme schopni zajistit 60 až 70 % klimatizačních potřeb závodu,“ vysvětluje Petr Mazal.
Po realizaci uvedených plánů bude zbývat ještě eliminovat denní spotřebu zhruba 60 m3 plynu, který se používá v práškových lakovnách. „Zde hledáme ekonomické řešení, protože elektrická pec vychází velmi draho a tzv. zelený plyn je také velice drahý,“ podotýká Petr Mazal. Je ale mnoho dalších věcí, které podle ředitele závodu lze změnit snadno a levně. Zaměstnanci jsou například neustále školeni v tom, jak třídit odpad. Zrušeny byly jednorázové obaly – PET lahve v automatech či plastové kelímky na kávu. Redukováno bylo také skládkování a komunální odpad se začal vozit do spalovny. Od nového roku tedy bude závod moci deklarovat snížení potřeby skládkování o více než 80 % s cílem dosáhnout v nejbližším období 0 tun. Pracuje se i na snižování spotřeby elektřiny. V závodě se používají vypínatelné zásuvky a stroje se nenechávají ve stand-by režimu. V letních měsících působí jisté potíže – ostatně jako téměř všude – klimatizace. Závod si proto musí u svého distributora elektřiny rezervovat tzv. patnáctiminutová maxima. „Nainstalovali jsme proto na hlavní elektrické přívody tzv. energy management. Systém zaznamenává jednotlivé spotřeby, které potom slouží pro optimalizaci spouštění jednotlivých technologií,“ popisuje Petr Mazal.
Dalším úsporným opatřením je instalace vlastních odbočných skříní s datovým přenosem do výrobního provozu, které informují o tom, jaká je spotřeba elektřiny na jednotlivých strojích. Na základě toho pak lze upravit provoz stroje či výrobní program.
Základem spokojení zaměstnanci
„Zaměstnanci jsou základním stavebním kamenem úspěchu a nám velmi záleží na tom, aby byli na pracovišti po všech stránkách spokojeni. Snažíme se o ně starat, jak jen to jde,“ zdůrazňuje Petr Mazal. S tím, jak se na pracovištích rozšiřují nové technologie, se vedení závodu snaží vybavovat zaměstnance novými kvalifikacemi, aby je byli schopni obsluhovat.
Ve spolupráci s místní Středí školou technickou Mohelnice si například závod sám rekvalifikuje elektrikáře, protože na trhu práce lidé s požadovanou kvalifikací zkrátka nejsou. Po absolvování tohoto kurzu se pak tito elektrikáři mohou ihned zapojit do montáže nových technologií. Se zmíněnou střední školou mohelnický závod ostatně spolupracuje dlouhodobě, jeho mistr se například ve škole coby člen komise účastní závěrečných zkoušek. Mohelnický závod se věnuje rovněž nezištným aktivitám: sponzoringu regionálních společenských akcí, například hudebního festivalu Fingers Up, či charitativní podpoře. V rámci vlastního sociálního programu spolupracuje například s dětským centrem Ostrůvek či s Charitou Zábřeh.