To, co podniky doopravdy potřebují, není teorie, ale konkrétní produkt (řešení a nástroje), který by obsahoval vzájemně dobře sladěná softwarová a automatizační řešení. Z tohoto požadavku vycházeli odborníci ze společnosti Siemens, kteří se podíleli a podílejí na vytváření sady nástrojů a řešení pro digitální podnik – Siemens Digital Enterprise Suite.
K digitalizaci celého průmyslového výrobního procesu s přidanou hodnotou se využívá centrální datová platforma, jednoduchou výměnu dat v rámci jednotlivých výrobních modulů a průběžné sbírání provozních dat zajišťují chytré průmyslové komunikační sítě. Portfolio řešení a nástrojů Siemens Digital Enterprise Suite je sestaveno tak, aby s ním zákazníci mohli ihned začít investovat do kroků vedoucích k postupné implementaci Průmyslu 4.0. Vhodné je pro použití na všech úrovních výrobního provozu. Propojení strojů mezi sebou navzájem a také se systémy vyšší úrovně umožňuje centralizaci zdrojů a výrobních dat. Přínosy tohoto řešení se projeví především ve snížení nákladů při realizaci objednávek. Přístup k informacím o objednávkách napříč celou firmou umožňuje vytvořit optimální strategie pro přidělování objednávek různým výrobním lokacím v rámci firmy. Kromě toho řídicí pracovníci na první pohled vidí zásoby materiálu, logistické operace a dostupnost nástrojů, a celou výrobu tak mohou účinně koordinovat.
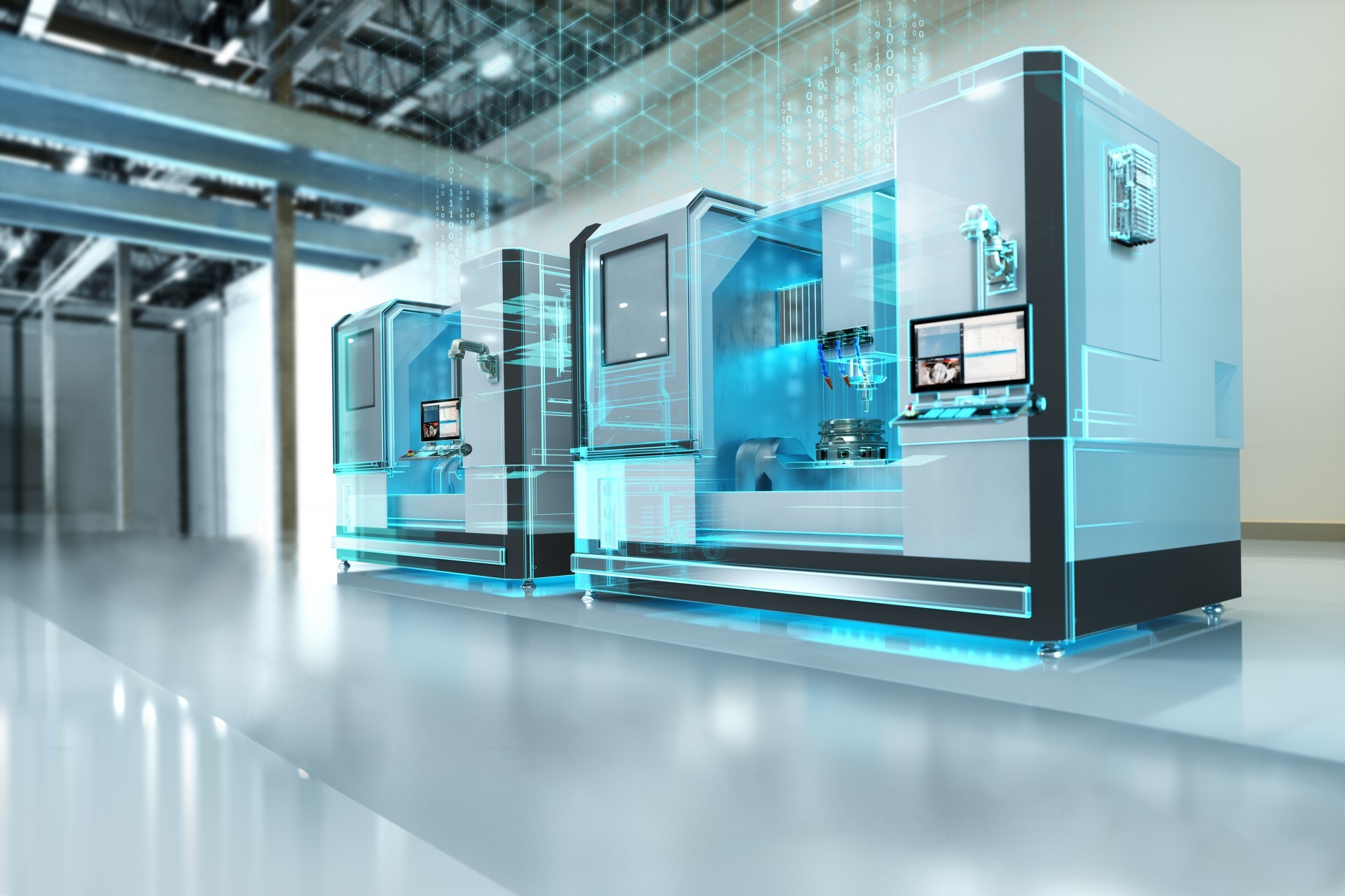
Vyšší kvalita i produktivita
Obrovský potenciál mají digitální dvojčata také v oblasti řízení kvality, poněvadž umožňují mnohem lépe vedenou dokumentaci výrobních postupů a výrobních parametrů. Pokud výrobci přesně vědí, jaká součást s jakými parametry a do jakého produktu byla nainstalována, mohou velmi přesně odhadnout možné problémy, včas na ně reagovat a výrobu mnohem lépe optimalizovat. Ve výrobním závodě v německém Amberku, kde Siemens vyrábí řídicí systémy pro automatizaci Simatic, zajistilo využívání komplexního systému dokumentace a hodnocení extrémně nízkou chybovost ve výrobě. Také ve zpracovatelském průmyslu je využití digitálních dvojčat cestou k vyšší efektivitě a produktivitě. Posun od integrovaného inženýringu k integrovaným provozům, který Siemens udělal, otevřel firmám ve zpracovatelském průmyslu možnost sestavit si komplexní datový model od návrhu výrobního závodu až po jeho provoz. I v této oblasti je digitalizace zárukou kratší doby uvedení na trh, větší flexibility a vyšší efektivity. To vše je pro tyto společnosti příležitostí rychle a správně reagovat na volatilitu a změny na globálních trzích a zvýšit vlastní produktivitu a stejně tak i energetickou účinnost a efektivitu nakládání se zdroji.
Vše na jedné platformě
Portfolio digitálních datových služeb Siemens doplňuje MindSphere – cloudový otevřený operační systém pro internet věcí, který vzájemně propojuje stroje a zařízení, výrobní systémy, řízení i celé závody a prostřednictvím pokročilých analytik umožňuje využívat bohatství dat generovaných internetem věcí (IoT). MindSphere ale také slouží jako platforma pro vývoj nových digitálních obchodních modelů pro průmyslové firmy. Nabízí nejmodernější bezpečnostní funkce pro sběr dat v terénu a pro přenos a ukládání těchto dat v cloudu.
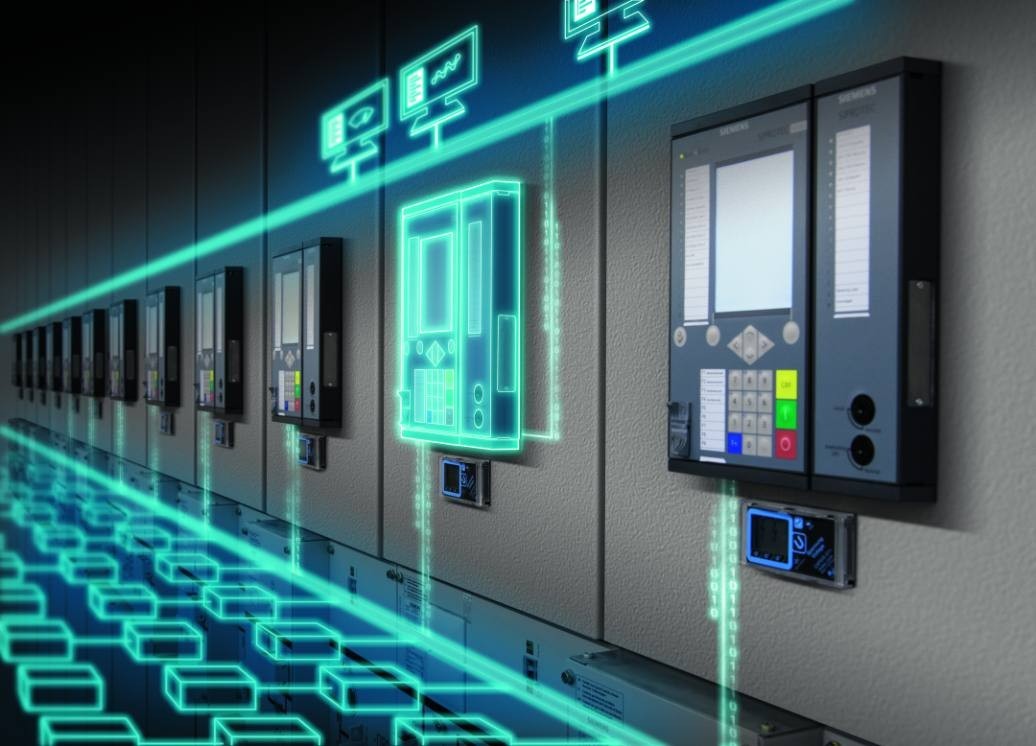
Digitální dvojče pro elektromotor
Už za pár let budou mít elektromotory vyráběné v závodě Siemens v Mohelnici svá virtuální dvojčata, tedy přesné kopie ve virtuálním prostředí, která konstruktérům umožní sledovat bezpočet parametrů a také to, jak se vzájemně ovlivňují. Vývoj a testování programu digitálního dvojčete probíhá na HUB Ostrava ve spolupráci se specialisty z mohelnického a frenštátského závodu. Odborníci na elektroniku a mechaniku z obou závodů museli absolvovat intenzivní školení zaměřené na práci v prostředí simulačních programů. Prvním krokem je vytvořit veškeré fyzikální modely existujícího motoru, spustit výpočty a zkontrolovat jejich kompatibilitu. Například jestli teplotní model komunikuje s elektromagnetickým modelem apod. V dalším kroku se ověří výsledky simulací testováním na zkušebně a sladí se případné odchylky. Tím by měl vzniknout nástroj, který bude v budoucnu pomáhat vyvíjet nové řady elektromotorů efektivněji a levněji. Jeden model, který propojí všechny oblasti vývoje, dokáže odhalit možné chyby ještě před zavedením motoru do výroby. Už nebude nutné ve zkušebně těžce simulovat všechny podmínky, ve kterých motor pracuje, a nebudou se ani muset vyrábět vzorky motorů. Díky tomu se budou moci dodávat nové výrobky na trh rychleji. Usnadnit by se měl i proces certifikace. S využitím digitálních dvojčat se počítá také v oddělení technologického vývoje. Konstruktéři a projektanti nejdříve musí pracně převést všechny 2D modely na 3D modely. Až poté mohou přistoupit k „oživování“ 3D modelů. Jakmile je rozhýbou, mohou začít s ověřováním fyzických parametrů stroje, technologických celků, ověřovat dosahy manipulátorů a robotů, návaznosti technologií na sebe, průběžnou dobu výroby v uzlu včetně manipulace apod. Budou schopni si nasimulovat požadované vstupní a výstupní parametry výrobních uzlů a pracovišť předtím, než koupí nový stroj a začnou ho uvádět do provozu. Tato příprava v budoucnu pomůže maximálně zkrátit fázi implementace technologií do výrobního procesu. Na tříletý projekt tvorby digitálního dvojčete získal Siemens grant od Ministerstva průmyslu a obchodu ČR.