Během posledních let se aditivní výroba vyvinula do podoby nezávislé výrobní strategie, která umožňuje vytvářet zcela nové typy komponent a struktur v malých výrobních sériích i v plně customizovaných prototypových variantách.
Technologie 3D tisku umožňuje vyrábět podvozky pro závodní auta, složité komponenty pro letecké motory, tělní implantáty nebo lopatky plynových turbín. Efektivní je i ve výrobě náhradních dílů pro stroje či vozidla, která již po celá desetiletí fungují například v elektrárnách či jezdí po železnici a očekává se, že ještě dalších mnoho let budou. Nejen z těchto důvodů proto není divu, že je 3D tisk považován za klíčovou průmyslovou technologii budoucnosti. Ve výrobě na tradičních obráběcích strojích existují limity z hlediska geometrie obráběných dílů. Jinými slovy, na obráběcích strojích nemůžete vyrobit vše, tedy každý tvar. V tomto ohledu naopak 3D tisk nezná hranic. Designéři si zde mohou vymyslet a navrhnout libovolně složitou strukturu. To znamená, že tvar součásti může být navržen plně podle požadované budoucí funkce. Příkladem jsou vnitřní chladicí kanálky, které pomáhají ochlazovat komponenty, které jsou vystavovány vysokým teplotám, jako je tomu u částí plynových turbín. Na druhou stranu ale ani 3D tiskem nelze vyrobit vše. Díky možnosti využívat různé netradiční materiály a různé materiálové kombinace je možné vyrábět komponenty lehčí a s novými fyzikálními vlastnostmi, nicméně právě fyzika je to, co omezuje i tento jinak vysoce flexibilní proces. Technologie 3D tisku obecně a vnitřní prostředí 3D tiskáren má jasné fyzikálněchemické parametry, a ty představují meze určující, jaké materiály lze používat a jaké fyzikální vlastnosti nakonec bude mít výsledný produkt. Aditivní výroba proto pravděpodobně nikdy plně nenahradí výrobu subtraktivní. Vše nasvědčuje tomu, že se tyto technologie budou v budoucnu čím dál tím více vzájemně doplňovat. Tento trend můžeme vidět již dnes na příkladu tzv. hybridních obráběcích strojů, které jsou něco jako „dva v jednom“.
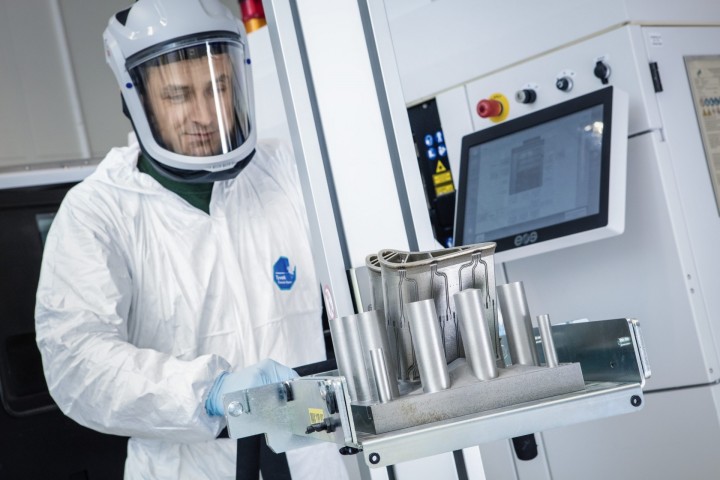
Aditivní výrobu řídí data
Současný obrovský pokrok v aditivní výrobě by sám o sobě nebyl možný bez komplexní digitální transformace výrobních procesů od návrhářského a výrobního softwaru přes simulační nástroje pro 3D tisk až po řízení a monitorování samotných 3D tiskáren. Všechny tyto prvky musejí do sebe přesně zapadat. Aditivní výroba, především kovových součástek, ale v současnosti bohužel stále ještě nefunguje tak hladce, jak by si uživatelé přáli. Než se technologové propracují k ideálnímu výrobnímu postupu, procházejí řadu iterací, kde je každá z nich posune o kousek blíž ke stanovenému cíli – přesným rozměrům a požadovaným materiálovým vlastnostem. Týká se to především nastavení parametrů tisku, jako je rychlost nebo výkon laseru. To se obvykle nikdy nepodaří napoprvé, protože často dochází k lokálnímu přehřátí nebo deformacím, které buď přímo ovlivňují výrobní proces anebo dokonce způsobí, že je součást dále nepoužitelná. Vysoce efektivním řešením je optimalizace procesu ve virtuálním prostředí a teprve až pak jeho praktická realizace. Za tímto účelem vyvinuli odborníci ze společnosti Siemens v rámci systému NX nový softwarový modul založený na algoritmech, které umožňují předpovídat přehřívání i deformace. Beta verze tohoto modulu se v současnosti testuje v několika velkých firmách, např. Honeywell a Toolcraft, a Siemens Power Generation, Power Services a Material Solutions. S tímto produktem se dostáváme mnohem blíže k cíli, kterým je bezchybně a napoprvé vytisknout produkt přesně tak, jak byl navržen v CADu.
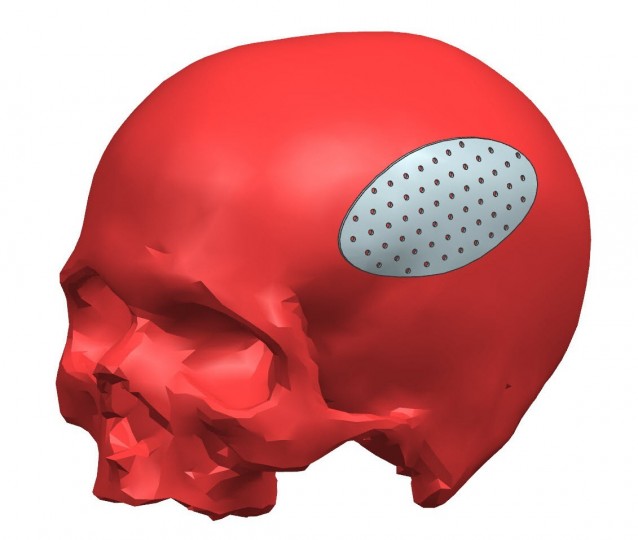
Významnou skupinu aplikací 3D tisku představuje výroba tělních implantátů. Tato nová technologie umožňuje vyrábět implantáty přesně na míru konkrétnímu pacientovi a současně z tzv. exotických materiálů, které dříve použít nešly.
3D tisk jako součást výrobního procesu
Průmyslové 3D tiskárny a příslušný software ale samozřejmě netvoří celý příběh. Společnosti v budoucnu budou muset pečlivě zvažovat, jak co nejlépe začlenit aditivní výrobu do svých vlastních výrobních procesů. 3D tisk by jim mohl pomoci, aby se staly agilnějšími například tím, že budou tisknou určité komponenty pouze na požádání místo toho, aby je držely skladem. Díky tomu budou flexibilnější a navíc ušetří místo. Důležitou součástí celého procesu je i uchovávání konstrukčních dat v cloudu. To otevírá slibnou budoucnost, ve které společnosti budou schopny tisknout komponenty kdekoli – například ve vzdálených regionech, kde by zákazníci jinak museli čekat dny nebo i týdny, než by se k nim dostaly náhradní díly. To ale samozřejmě za podmínky, že bude plně zaručena bezpečnost digitálních výrobních plánů uložených v cloudu.
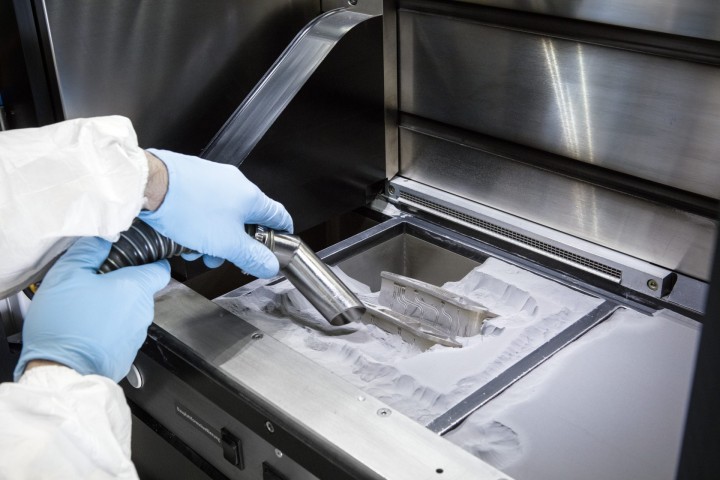
Pro 3D tisk kovových strojových součástí se nejčastěji používá tisk z práškového lože. Snad se brzy dočkáme tisku „na stisknutí tlačítka“.
Tisk na stisknutí tlačítka?
Aditivní výroba nabízí průmyslu příležitost k vytvoření nové výrobní cesty, která má jedinečný potenciál. Navzdory nespočetným možnostem ale tato technologie dosud nedosáhla takové úrovně, aby bylo možné vytisknout požadovanou komponentu pouhým stisknutím tlačítka. Cestu od návrhu k hotovému produktu ještě zdaleka není v tomto oboru rutinní záležitostí. A přitom rutina je obzvláště důležitá, pokud jde o tisk z kovu, kde se předpokládá, že koncové produkty mohou být využívány v náročných provozech – například motory nebo turbíny. Vývoj v tomto směru ale pokračuje dál s velkou intenzitou a dosažené pokroky jsou velké. Průmyslového 3D tisku „na stisknutí tlačítka“ se tedy pravděpodobně dočkáme již velmi brzy.
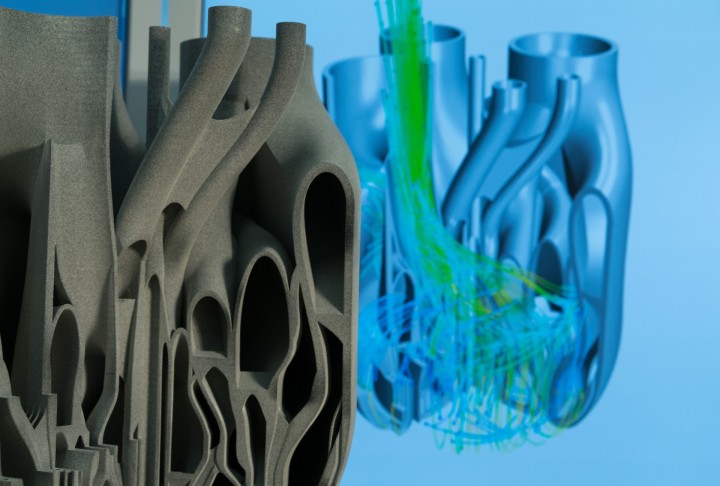
Digitální dvojče
Ústředním prvkem na cestě k digitální továrně je digitální dvojče, které prostupuje celým procesem výroby produktu. Reprezentuje složité geometrie, umožňuje simulace a dá se použít pro širokou škálu výrobních postupů 3D tisku. Díky němu se již nemusejí provádět časově náročné a choulostivé konverze mezi různými datovými formáty. Kromě toho, žádná změna se již neprovádí izolovaně. Pokud simulace odhalí, že je potřeba provést určité opravy, tyto informace jsou ihned začleněny do digitální šablony produktu nebo komponenty, která se má tisknout. Výsledkem je, že proces, který by normálně trval rok, lze zvládnout v horizontu několika týdnů. Cíl vyrábět produkty, které budou již po prvním vytištění vhodné pro sériovou výrobu, „na první dobrou“, je již na dosah.