V blízké budoucnosti budou v továrnách pracovat výrobní linky, které budou schopny se samy nastavovat a samy si koncipovat vlastní výrobní program. Že to zní jako science fiction? Omyl, tato doba se již velmi rychle přibližuje a její příchod doprovázejí digitální dvojčata.
Jedním z nejzávažnějších problémů současné výroby je skutečnost, že projekční týmy používají jiné systémy než samotná výroba. V praxi to může znamenat, že konstruktéři předají svoji hotovou práci lidem z výroby, kde se začne vytvářet plán následného zpracování, avšak pomocí softwaru, na který jsou sami zvyklí. V rámci tohoto scénáře, který je bohužel celkem obvyklý, pak hrozí ztráta synchronizace dat a vzniká prostor pro možná selhání a vznik chyb.
Problémy se ale objevují i v etapě návrhu prostorového uspořádání výrobního provozu. V současnosti se stále často pracuje pouze s 2D půdorysy a papírovými plány, což je náročné z hlediska času i vynaloženého úsilí. I když se jedná o podstatnou část celého procesu, jsou tato řešení dost nepružná a často se setkáváme i s tím, že se změny uspořádání provozu v příslušných plánech vůbec neobjeví. To může způsobit problémy zejména v případě rychle se měnících odvětví, například v oblasti spotřební elektroniky, kde je nutné výrobní systémy neustále rozšiřovat a obnovovat.
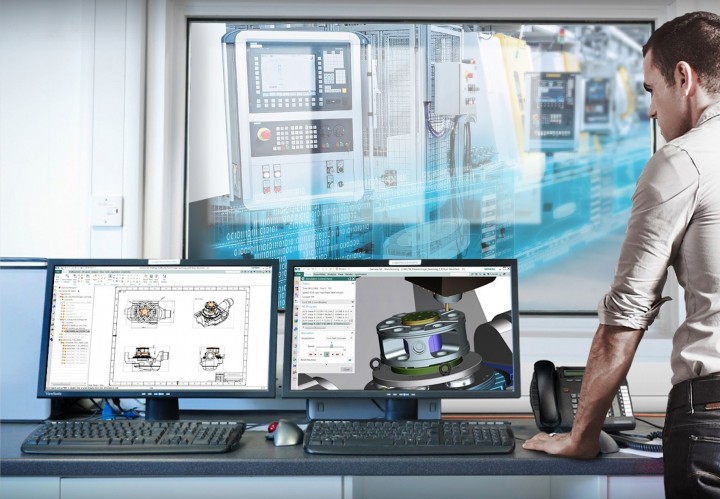
V návaznosti na uspořádání provozu pokračují práce na zajištění výroby obvykle validací procesu. I zde se setkáváme s potenciálně významnou překážkou bránící dosažení efektivity. Výrobci obvykle čekají, až bude na místě skutečné vybavení, aby zjistili, jak bude doopravdy fungovat. Nesplňuje-li pak výsledek jejich očekávání, bývá už pozdě hledat jiná alternativní řešení.
Vzhledem ke složitosti moderního výrobního provozu a často i nedostatečné koordinaci mezi jednotlivými aplikacemi a plánovacími systémy může být obtížné vymezit oblasti nebo články ve výrobě, které zdržují celou linku. A jakmile dojde na poslední článek celého řetězce, samotnou výrobu, bývá často obtížné změřit efektivitu a zjistit, zda realita odpovídá plánům. I zde je problémem především komplexnost celého systému a také problematické poskytování zpětné vazby z výrobního provozu.
Koncept digitálního dvojčete
Všechny výše zmíněné problémy pomáhá řešit koncept tzv. digitálního dvojčete. Jedná se v podstatě o repliky již existujících anebo zatím pouze navržených reálných věcí ve virtuálním světě. Taková dvojčata mohou být navržena nejen pro konkrétní produkty, ale i pro celé výrobní systémy.
Aby výrobní podniky mohly zajistit podmínky pro tuto plně flexibilní výrobu, potřebují velké množství dat – sesbíraných v reálném čase a vypovídajících o tom, jaké komponenty jsou zapotřebí kde a kdy, jak zpracovat ten který díl a jaký vliv by měly různé. Zatím jsou to ale stále lidé, kdo musí strojům říkat, co mají dělat. „Říkají“ jim to prostřednictvím řídicích kódů, které píší programátoři na základě simulací vytvářených v PLM softwaru (Product Lifecycle Management). K tomu potřebují vědět, kde je který stroj umístěn, jak jsou jednotlivé stroje vzájemně seskupeny anebo jaká je servisní historie každého z nich. Tyto informace musí mít programátor k dispozici ještě před tím, než je začne přeprogramovávat a reorganizovat do nových konfigurací. De facto je tedy potřeba spojit současné procesy v továrně s těmi, které zde budou probíhat v budoucnu.
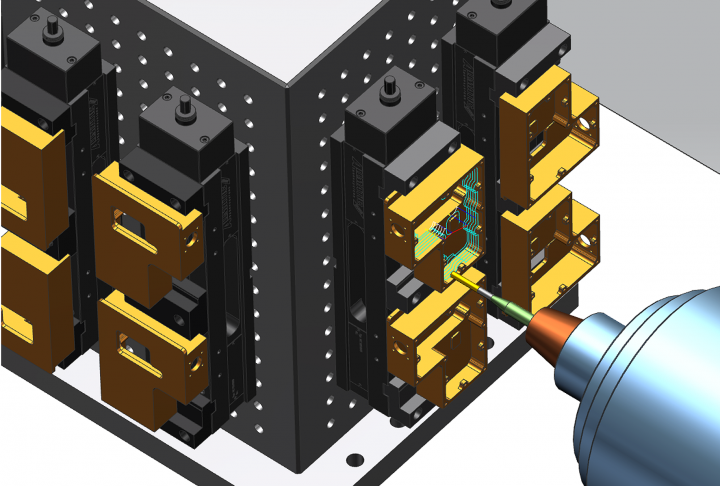
Jak to vlastně funguje?
Pomocí softwaru NX (anebo jiných systémů CAD) můžeme vytvořit model výrobku a otevřít jej jako 3D JT model v produktu Teamcenter (Siemens PLM software). Software může během několika sekund vytvořit tisíce variací daného produktu, jako kdyby proběhla jeho fyzická výroba. K tomu využívá techniky zpracování velkých objemů dat (tzv. big data), popisy produktů, výroby a informací (PMI), které specifikují tolerance a součásti produktu. Pracuje ale i se základním popisem výrobního procesu, aby mohl včas odhalit nebezpečí případných kolizí.
Digitální dvojče může také zlepšit spolupráci mezi projekčními a výrobními týmy, takže lze lépe naplánovat další kroky a určit jaké jsou k tomu potřebné zdroje. Pokud jde o prostorové uspořádání výrobního provozu, je možné vytvořit digitální dvojče se všemi detaily ohledně mechanizace, automatizace a zdrojů – a pevně je provázat s návrhem produktu a výrobním ekosystémem. Dojde-li např. ke změně produktu, vyžadující použití nového robota, technici provádějící simulaci uvidí to, zda robot nebude vzhledem ke své velikosti kolidovat s jedním z pásových dopravníků. Technik plánující uspořádání provozu pak může provést potřebnou úpravu a vystavit požadavek na změnu, upozorňující nákupčí na potřebu pořízení nového vybavení.
Digitální dvojče je možné využít i ke statistickému simulování a vyhodnocení plánovaného výrobního systému. Dokáže vyhodnotit, zda je lepší nasadit lidi, roboty nebo jejich kombinaci. Je možné simulovat všechny pracovní postupy – a zjistit tak dokonce i to, kolik energie spotřebuje výrobní vybavení.
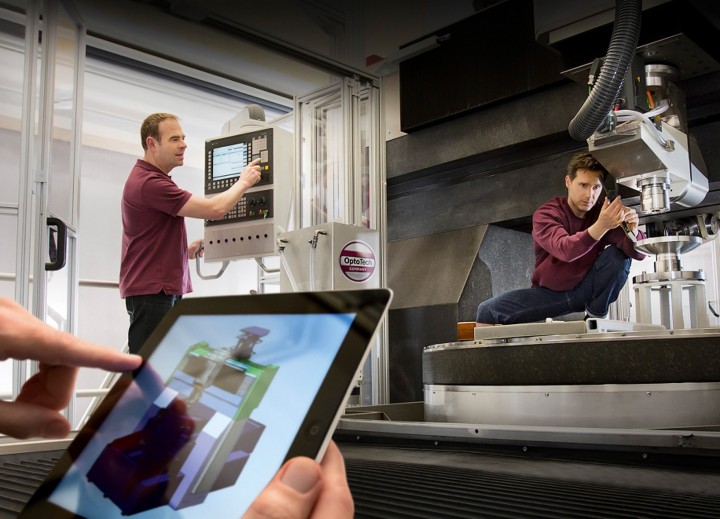
Copy-Paste výrobní systémy
Uživatelé mohou s pomocí PLM softwaru a vytvořených digitálních dvojčat vyřešit prakticky libovolný scénář. Například, když se podnikový management rozhodne rozšířit své výrobní kapacity a postavit další výrobní halu, aby zdvojnásobil objem výroby, PLM software mu umožní „zkopírovat“ si stávající výrobní systémy a „vložit“ je do jiného prostoru. V podstatě lze tímto způsobem vytvořit identické výrobní zařízení kdekoli na světě a ihned začít vyrábět se stejnou kvalitou i přesností.
Dá se očekávat, že umělá inteligence bude v budoucnosti hrát v PLM stále větší roli. V současné době se nacházíme uprostřed vzrušujícího vývoje, v němž stále narůstá schopnost strojů učit se. Výsledkem toho je, že největší výzvou, jíž automatizace v současné době čelí, je naučit stroje psát si samy nové řídicí kódy. Přestože v této situaci ještě nejsme, již teď přesně víme, jak se to stane.