Výrobce kompresorů, společnost SECOP ve Zlatých Moravcích na Slovensku, potřeboval zvýšit kapacitu výrobní linky a zlepšit monitoring procesů. Papírové výkazy se přežily a vedení firmy zaujaly možnosti, které přináší koncepce Průmysl 4.0. Jako první krok k ní a zároveň jako zkušební test, co digitalizace skutečně může firmě přinést, se rozhodli vytvořit digitální dvojče jedné z výrobních linek. A jaký je výsledek? Lepší nad očekávání! Úspěšný projekt na platformě Siemens navrhla a realizovala SIDAT DIGITAL dceřiná firma společnosti SIDAT.
Společnost SECOP je součástí stejnojmenného nadnárodního koncernu s pobočkami v Německu,Rakousku a v Číně. Ve slovenském závodě,kde pracuje okolo tisícovky zaměstnanců,vyrábějí hermetické kompresory pro lednice a chladicí vitríny do celého světa.Před rokem zde instalovali digitální dvojče pro výrobní linku NL. Cílem bylo zvýšení produkce linky o 15 % a získání zkušeností s digitalizací výrobního procesu.
Jednoduché informace pro vedoucího směny
Digitální dvojče navrhla společnost SIDAT DIGITAL, která má s podobnými projekty značné zkušenosti. Řešení navržené na platformě Siemens šetří díky zvýšení efektivity výroby ročně desítky tisíc eur. Prvním krokem k tomu bylo on-line sledování procesu výroby. Povedlo se jej zajistit propojením digitálních výstupů z výroby na velkoplošné LCD monitory, umístěné přímo ve výrobě. Na nich lze sledovat monitoring hodinové produkce, který je důležitý pro průběžné porovnávání a vyhodnocování efektivity provozu. V případě jejího poklesu je možné okamžitě hledat příčiny a zjednat nápravu. Software pro rychlý přehled na dílně používá grafiku s barevnými emotikony, podle nichž pracovníci i vedoucí směny okamžitě vidí, zda výroba probíhá v pořádku, nebo někde dochází ke zdržení. Reporty a on-line tabule zobrazují také prostoje a mikro prostoje. Do budoucna budou sloužit i k predikci možných problémů, kterým tak bude moci předejít.
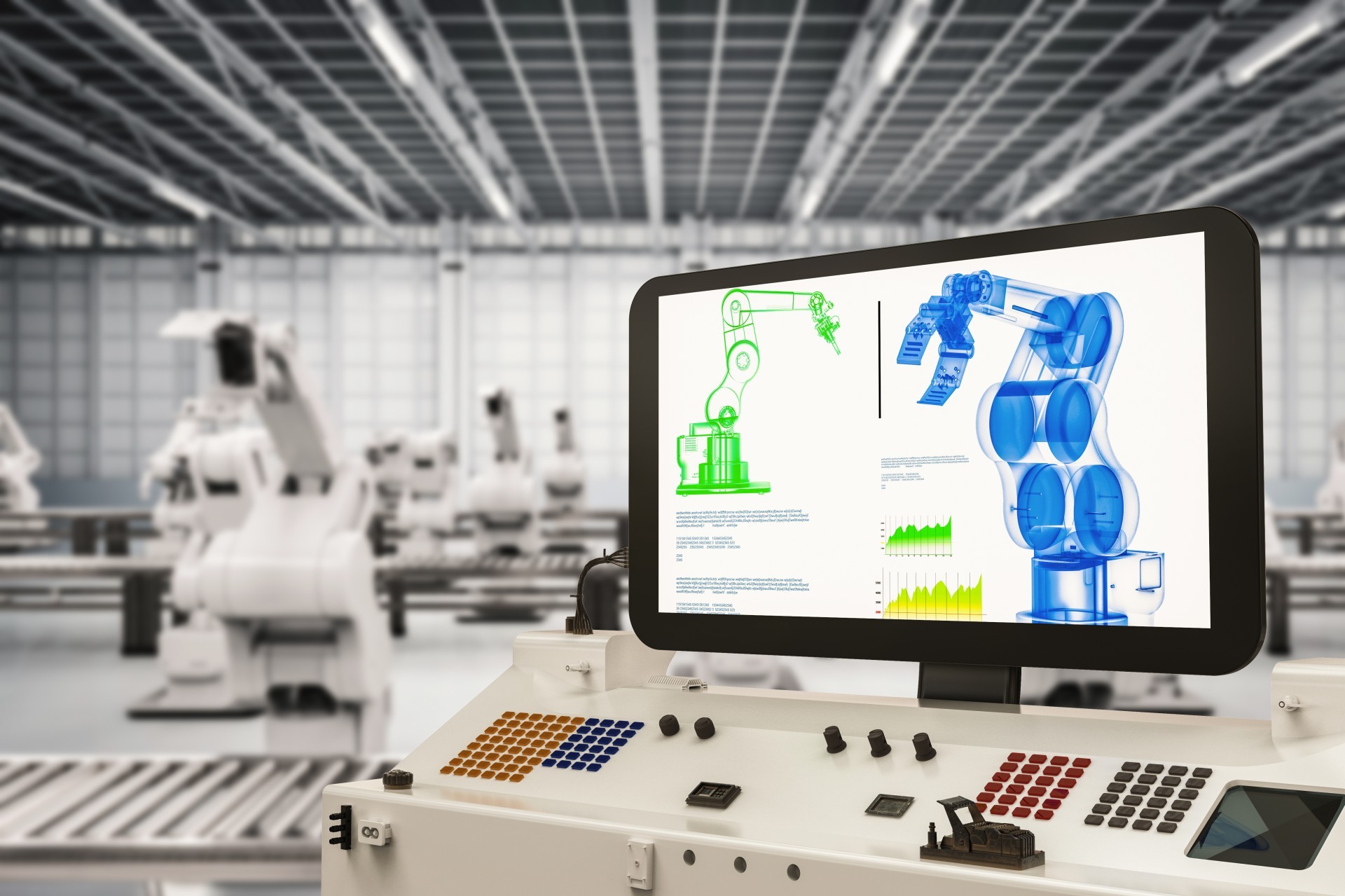
Jediná sekunda přinesla úsporu 50 tisíc eur
Další úsporu přineslo zavedení monitoringu cyklových časů, které se liší na různých částech linky a také podle vyráběných typů kompresorů. Podařilo se tak identifikovat problém v jednom kroku balení hotového produktu.Manipulační a balicí stroje nebyly ideálně sladěny a v taktu se rozcházely o jednu sekundu. Tak malá odchylka byla pouhým okem takřka nepostřehnutelná. Její odstranění však přineslo lepší synchronizaci navazujících kroků,zvýšenou efektivitu a výslednou úsporu téměř 50 tisíc eur ročně.Cyklový čas se dříve měřil při pravidelném přeměřování jednou za roka úzká místa ve výrobě se definovala teoreticky. Každodenní praxe se aleod reality často lišila. „Proto jsme se rozhodli pro digitalizaci, která nám pomáhá monitorovat klíčové ukazatele výroby během celého roku nonstop.Díky tomu teď nepracujeme s odhady,ale s fakty a daty,“ vysvětluje František Šlosiar, Stator & Electrical Equipment Production ze společnosti SECOP. Při výrobě navíc často docházelo k mikro zastavením, která ve výsledném součtu výrazně snižovala plynulost a efektivitu výroby. Díky digitálnímu dvojčeti a monitoringu cyklových časů se podařilo úzká místa na lince odhalit a zjednat nápravu.Podařilo se také identifikovat stroj s největší poruchovostí, jímž byl lis na čerpadla. „Problém jsme vyřešili zdvojením stanic pro dvě samostatné platformy. Ušetříme až 20 minut prostojů za směnu, což je roční úspora téměř 20 tisíc eur,“ říká František Šlosiar.
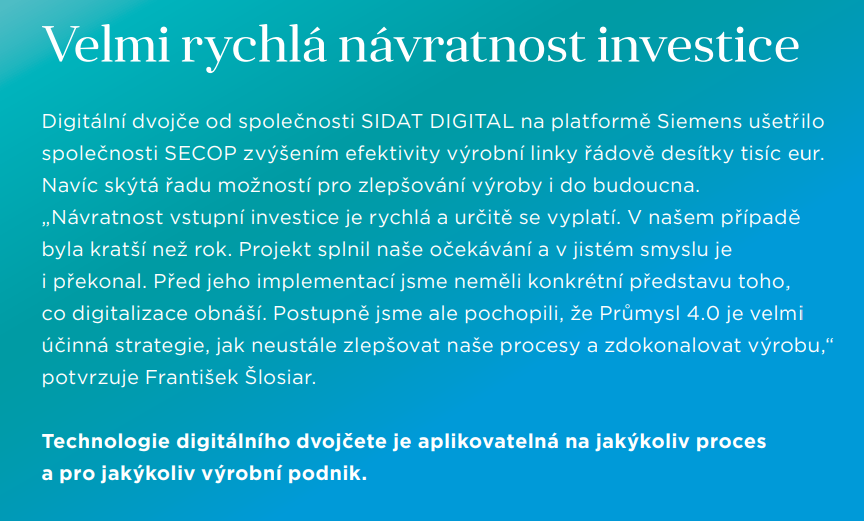
Proč stojí linka? Digitální dvojče poradí
Digitální dvojče linky je postaveno na platformě Tecnomatix od společnosti Siemens a jejím konceptu digitální továrny. Jedná se o unikátní a komplexní řešení, které dokáže propojit reálný a virtuální svět výroby. „Pro technologii Siemens jsme se rozhodli proto, že je to ucelená platforma a umožňuje propojení automatizačních prvků, které jsou na špičkové úrovni, s digitalizačními nástroji,“ vysvětluje Robin Mitana, jednatel společnosti SIDAT DIGITAL. Digitální dvojče umožňuje prohlédnout si aktuální výrobu, která na lince probíhá, ale i porovnat reporty za uplynulé období. Porovnání reportů z digitálního dvojčete a skutečné výroby umožňuje odhalit různé odchylky od plánované výroby, identifikovat důvody a zapracovat na jejich odstranění do budoucna. Výstupem z digitálního dvojčete linky jsou grafy blokování výroby, na kterých je přehledně graficky zobrazena počáteční příčina problému, který se na lince vyskytl, a úzká místa výroby, která bránila plynulému provozu. Systém sbírá data z výroby a analyzuje je. Lze tak krok za krokem monitorovat, zda proces běží podle nastavených parametrů. V případě odchylek je možné identifikovat problém a odhalit jeho příčinu: například zpoždění nebo nedostatečnou kapacitu konkrétního stroje v lince. Tu pak lze odstranit. „Detailní data cyklových časů můžeme zohledňovat i při manuální výrobě, jejíž variabilita je obrovská, protože nezávisí jen na strojích, ale i na lidském faktoru. Můžeme tak sledovat a objektivně hodnotit i práci operátorů,“ vysvětluje František Šlosiar ze společnosti SECOP. Další report, který digitální dvojče poskytuje, je přehled využitelnosti strojů. Systém také umožňuje sledovat pohyb každého vyráběného kusu na lince. Funkcionalita je velmi potřebná pro interní výrobní proces i zpětnou vazbu od zákazníků.
Řešení navržené na platformě Siemens