Obří letadlo Boeing 747 se při startu odlepí od ranveje při rychlosti 280 km/h. Supersportovní automobil Bugatti Chiron jezdí i rychlostí nad 400 km/h a samozřejmě se od země odlepit nechce. Bezpečnou jízdu mu zajišťuje vylepšená technologie 3D tisku od společnosti Siemens.
Sportovně laděné automobily nazvané svým jménem vyráběl konstruktér italského původu Ettore Bugatti v první polovině minulého století v alsaském městě Molsheim. Značka je mimochodem spojena s jednou z nejlepších a nejproslulejších závodnic světové historie, Češkou Eliškou Junkovou, která právě v těchto vozech ve 20. letech překvapovala celý svět svými výsledky na automobilových soutěžích. Poslední klasická „bugatka“ vznikla v roce 1952. O 46 let později značku koupil koncern Volkswagen a vyrábí pod ní sportovní vozy, a to opět v Molsheimu. Tedy přesně tam, kde svou výrobu Ettore Bugatti založil. Název posledního dvoudveřového sportovního vozu rovněž navazuje na historii. Louis Chiron byl špičkový monacký závodník, který začal jezdit na vozech Bugatti. Závodil do svých 59 let a ve starších českých slovních obratech se vyskytoval výraz „jezdí jako Chiron“, čímž se myslelo, že dotyčný se na silnici opravdu neloudá.
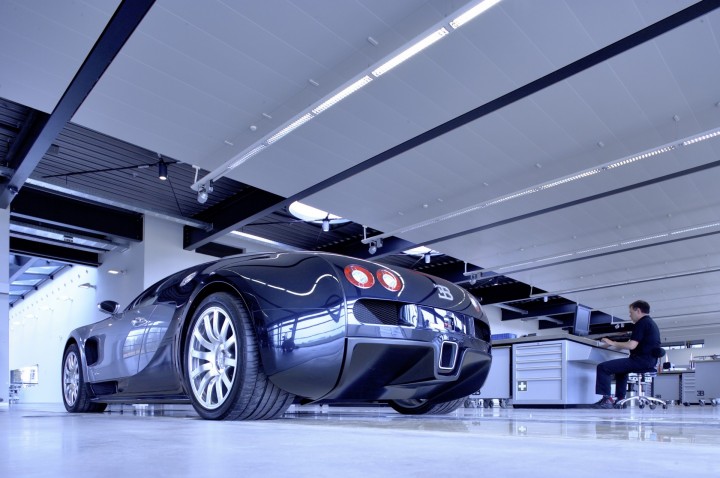
Povoleno „jen“ 420 km/h
Vůz Bugatti Chiron byl představen na autosalónu v Ženevě v roce 2016 a určitě to není tuctové auto. Má osmilitrový motor se čtyřmi turbodmychadly, výkonem 1 103 kW a točivým momentem 1 600 Nm. Z nuly na 100 km/h zrychlí za 2,4 sekundy, na 200 km/h za 6,5 sekundy a na 300 km/h za 13,6 sekundy. Maximální rychlost Chironu je z bezpečnostních důvodů elektronicky omezena na 420 km/h. Už u Chironova předchůdce, modelu Bugatti Veyron, a nyní opět použili konstruktéři aktivní aerodynamický systém, který umožňuje udržet takto silný a rychlý automobil na vozovce. Kontakt s jízdním povrchem je zajištěn hydraulicky ovládaným řídicím systémem, který reguluje přítlak vozu k silnici. Systém rozšiřuje a nastavuje zadní spoiler podle potřeby a stejně tak otevírá nebo zavírá difuzory – speciálně tvarované části podvozku, vzduchové kanály, jež zlepšují aerodynamické vlastnosti vozidla, urychlují proudění vzduchu pod vozem, a vytvářejí tak podtlak, který „přisává“ automobil k povrchu. Řídicí systém ovládá rovněž nastavení podvozku, aby vůz udržoval optimální úhel a vzdálenost od silnice. Výrobce spolupracoval s divizí Siemens Digital Factory na vývoji 3D tiskem vytvářených titanových součástek a ultralehkých tenkostěnných uhlíkových vláken. Při 3D tisku jsou trojrozměrné objekty vytvářeny z vhodného materiálu jakoby tiskem po vrstvách, takže mohou vzniknout unikátní objekty, které do detailu odpovídají konkrétním potřebám. Výsledkem spolupráce Bugatti a Siemens jsou titanové součástky, které dobře snižují odpor větru, součástky z uhlíkových vláken o 53 % lehčí než ty předchozí, anebo také hliníková středová konzole v palubní desce. Úspěch byl možný jen díky součinnosti hned několika společností, které se na výrobě Chironu podílejí. „Dnešní 3D tisk znamená propojení všech výrobních procesů od designu až po postprodukční úpravu do jednoho digitálního produkčního řetězce,“ říká Karsten Heuser z divize Digital Factory. Právě software od Siemens umožnil hladce navazující propojení všech přípravných i výrobních fází. Místo aby museli řešit kompatibilitu různých softwarů, mohli se konstruktéři a technici plně soustředit na přípravu konečného výrobku.
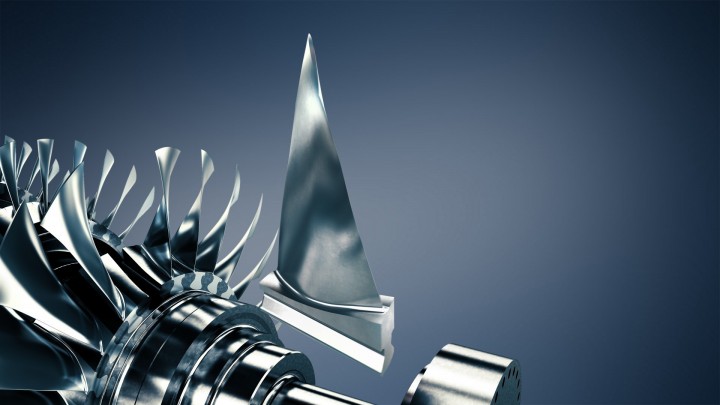
Začalo to turbínami
Siemens se na 3D tisku ale samozřejmě nepodílí jenom přípravou součástek pro supersportovní Bugatti. Pomocí 3D tisku sériově vznikají také například lopatky pro turbíny nebo složité hořáky pro plynové turbíny. Ty také ostatně stály na samém začátku aktivit společnosti Siemens v oboru aditivní výroby. První hroty hořáků pro plynové turbíny byly vyrobeny v 3D tiskárně společností EOS v roce 2013. V roce 2014 otevřela tehdejší divize Siemens Mobility v Erlangenu kompetenční centrum pro aditivní výrobu, které navrhuje a vyrábí náhradní díly pro železniční dopravu a také současně poskytuje poradenství zákazníkům. V roce 2016 společnost Siemens získala 85 % akcií ve společnosti Materials Solutions ve Velké Británii, jedné z předních světových společností orientované na aditivní výrobu. O rok později to byli právě technici ze Siemens, kteří jako první na světě úspěšně vytiskli a testovali lopatky plynové turbíny. Nedlouho poté byly lopatky následovány tištěnými hořáky ze závodu Siemens ve švédském Finspångu. Tyto hořáky úspěšně fungují v komerční plynové turbíně od roku 2017. V oblasti energetiky plánuje společnost Siemens vytipovat do roku 2025 celkem 200 komponent, které by bylo vhodné vyrábět pomocí 3D tisku.
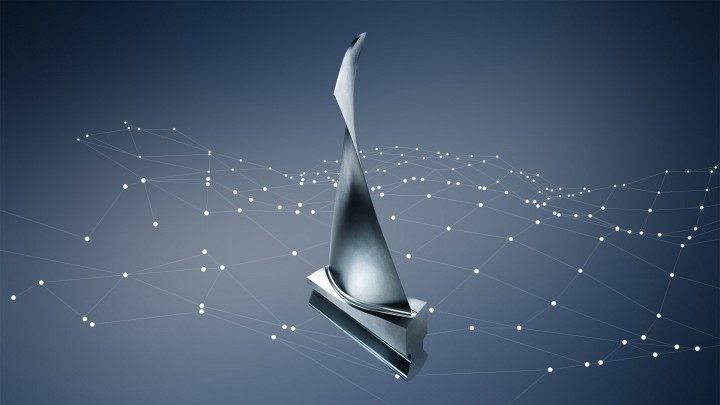